UNIVERSITATEA
DIN PITESTI
FACULTATEA
DE MECANICA SI TEHNOLOGIE
INGINERIE
ECONOMICǍ INDUSTRIALǍ
PROIECT
LA
Tehnologia Fabricarii
Produselor
Partea I PROIECTAREA TEHNOLOGIEI DE FABRICATIE
Analiza
functional - constructiva a piesei
Codificarea
si clasificarea suprafetelor piesei
Pornind de la desenul de executie al piesei " Bucsa"
s-au identificat urmatoarele suprafete :
simple, constituite
dintr-o singura suprafata (cilindrice, plane, conice si
elicoidale): S1, S2, S3, S4, S5, S6, S7, S8, S9, S10, S11, S14, S15, S16, S17;
complexe, formate din
reuniuni de suprafete generate simultan in timpul procesului de prelucrare
(caneluri, canal circular interior):S10, S11.
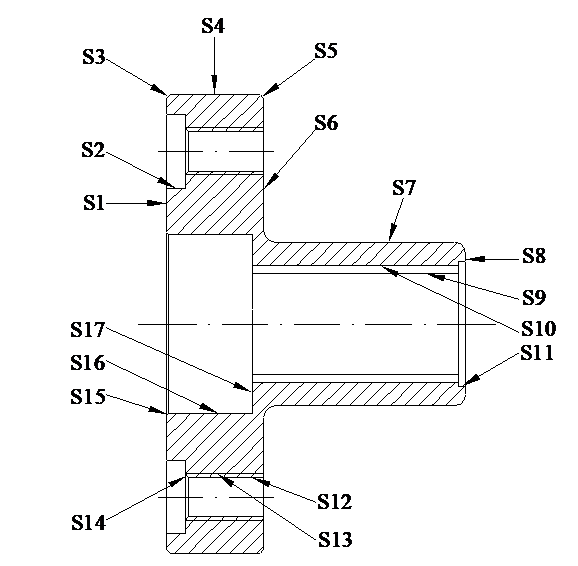
Figura
1.1-Suprafetele piesei
Caracteristicile
geometrice constructive prescrise piesei. Rolul functional al
piesei
Se analizeaza
caracteristicile geometrice constructive prescrise piesei. Fiecare
suprafata Sk se analizeaza din punct de vedere al :
caracteristicilor
dimensionale,
caracteristicilor de
forma (macro-geometrica si micro-geometrica - rugozitate),
caracteristicilor de
pozitie reciproca.
Rezultatele
analizei se prezinta in tabelul nr.1.1.
Tabel nr 1.1
Caracteristici geometrice
constructive ale piesei
Sk
|
Forma
|
Dimensiunile
caracteristice
principale
|
Treapta
de
precizie
|
Rugozitatea
Ra
[μm]
|
Toleranta
de
pozitie
|
Alte
caracteristici
|
S4
|
Cilindrica
exterioara
|

|
IT
11
|
|
|
|
S7
|
Cilindrica
exterioara
|

|
IT6
|
|
|
|
S2
|
Cilindrica
interioara
|
 
|
IT
13
|
|
|
|
S9
|
Cilindrica
interioara
|

|
IT13
|
|
|
Cota
libera
|
S12
|
Cilindrica
interioara(gaura)
|

|
IT13
|
|
|
Cota
libera
|
S16
|
Cilindrica
interioara
|

|
IT13
|
|
|
Cota
libera
|
S1
|
Plan
frontala
|
77/
|
IT13
|
|
|
Cota
libera
|
S6
|
Plan
frontala
|
25/ /
|
IT13
|
|
|
Cota
libera
|
S8
|
Plan
frontala
|
77/
|
IT13
|
|
|
Cota
libera
|
S17
|
Plan
frontala
|
22/ /
|
IT13
|
|
|
Cota
libera
|
S3,S5,S14
|
Conica
(tesitura)
|
1
x 45˚
|
IT13
|
|
|
Cota
libera
|
S15
|
Conica
(tesitura)
|
0,5
x 45˚
|
IT13
|
|
|
Cota
libera
|
S10
|
Complexa
(
canelura)
|
/ /2
|
IT8
|
|
|
|
S11
|
Complexa
(canal circular interior )
|
2/1/
|
IT13
|
|
|
Cota
libera
|
S13
|
Elicoidala
(filet)
|
M12X
1,25
|
|
|
|
Cota
libera
|
Rolul functional pe care suprafetele piesei il au in
subansamblul din care acesta face parte este sintetic prezentat in tabelul
nr.1.2.
Tabel nr.
1.2
Clasificarea
suprafetelor piesei
Categoria de suprafata
|
Codul suprafetei
|
Rolul suprafetei
|
|
S12, S13
|
Asigura fixarea piesei prin
suruburi
|
Tehnologica
|
S1, S2, S4, S6, S7, S8, S9, S10
|
Asigura orientarea piesei
|
S11
|
Pentru iesirea sculei din
prelucrare, evacuarea aschiilor
|
S3, S5, S14, S15
|
Asigura montarea
usoara a piesei in ansamblu
|
Libera
|
S16, S17
|
|
1.3.
Caracteristicile materialului piesei:
Materialul piesei " Bucsa" este OLC45. Acest otel este
destinat executiei pieselor tratate termic cu adancime de calire
garantata conform curbei de calibilitate a marcii. Caracteristicile
mecanice si compozitia chimica ale acestui otel sunt
reglemenate prin STAS 880-80 si sunt prezentate in tabelele 1.4,1.5
si 1.6, iar principalele domenii de utilizera in tabelul 1.3. Conform
standardului amintit, pentru otelul OLC45 sunt impuse:
Tabel nr. 1.3
Principalele domenii
de utilizare
OLC
45
|
Piese
tratate termic, de rezistenta ridicata si tenacitate
medie, ca: discuri de turbine, arbori cotiti, biele, coroane
dintate, volante, roti cu clichet, pene de ghidaje, melci pene,
flanse oarbe.
|
Tabel
nr. 1.4
Compozitia
chimica determinate pe otel lichid
Marca
otelului
|
Calitatea
|
Compozitia chimica %
|
C
|
Mn
|
S
|
P
|
OLC 45
|
|
|
|
Max0,045
|
Max
0,040
|
S
|
|
X
|
Max
0,035
|
Max
0,035
|
XS
|
|
Tabel nr.
1.5
Caracteristici
mecanice
Marca
otelului
|
Diametrul
probei de tratament
|
Felul
tratamentului termic
|
Limita
de curgere
|
Rezistenta
la
rupere
|
Alungirea
la rupere
|
Gatuirea
la rupere
|
Energia
de rupere
| |
OLC
45
|
|
N
|
|
Min
610
|
|
|
| |
OLC
45 X
|
|
CR
|
|
|
|
|
| |
OLC
45 XS
|
|
| |
Tabel nr.1.6
Caracteristici
mecanice
Duritate
Brinell
|
Marca
otelului
|
Tratament
termic
|
Domeniu
de dimensiuni
[mm]
|
Limita
de curgere
|
Rezistenta
la rupere
|
Alungirea
la rupere
|
Gatuirea
la rupere
|
Energia
de rupere
|
Normalizat
|
Recopt
|
OLC
45
|
CR
|
<=16
|
|
|
|
|
|
|
|
|
|
|
|
>16 . <=40
|
|
|
|
|
|
|
|
>40..<=100
|
|
|
|
|
|
|
|
Tratamentele
termice aplicabile acestei marci de otel sunt :
a) tratamente
termice primare, aplicate pe semifabricate cu grad redus de prelucrare :
recoacere de normalizare, recoacere de omogenizare, recoacere de
inmuiere;
b)
tratamente termice secundare (finale), aplicate pieselor finite :
calire, revenire, tratamente termochimice.Parametrii tratamentului termic.
Tabel nr.1.7
Parametrii tratamentului
termic
Marca
|
Stare
|
Recoacere
|
Normalizare
|
Calire
|
Revenire
|
OLC45
|
I
|
|
|
|
|
|
A
|
|
A-u
|
| | | | | | | | | |
unde: A-apa , u-
ulei.
Dintre caracteristicile
tehnologice ale unui material fac forjabilitatea, aschiabilitatea si
calibilitatea .
Forjabilitatea reprezinta capacitatea metalelor de a
se deforma si de a lua o forma noua sub actiunea
fortelor exterioare fara a se fisura. La oteluri, forjabilitatea
este cu atat mai buna cu cat continutul de carbon este mai redus,
astfel marca OLC 45 se poate aprecia ca are o forjabilitate buna.
Aschiabilitatea, este capacitatea materialelor de a putea
fi prelucrate prin aschiere cu ajutorul sculelor aschietoare. Otelurile
cu 0,3-0,6 C au aschiabilitate buna; continuturi mai mari de
carbon conduc la micsorarea vitezelor de aschiere. Continuturi
mai ridicate de S(<0,3%) si de P(<0,2%) in oteluri ,
imbunatatesc mult aschiabilitatea.Analizand aceste conditii
vom observa ca din punct de vedere al continutului de carbon, dar
si din cel al continutului de S si P, otelul OLC 45 are
aschiabilitate buna, pentru cresterea aschiabilitatii
este recomandata o recoacere prealabila de inmuiere.
Calibilitatea este proprietatea materialelor de a se
cali. Calibilitatea otelurilor creste o data cu
continutul de carbon si de elemente de aliere. Otelul OLC45
prezinta o calibilitate buna, pretandu-se la tratament termic al
suprafetei si la operatii de tratament termochimic.
1.4.
Tehnologicitatea constructiei piesei:
Tehnologicitatea
constructiei pieselor este caracteristica acestora de a se putea fabrica,
la programa de productie impusa, cu consumuri de materiale si
manopera reduse, la un cost cat mai mic. Aprecierea tehnologicitatii
constructiei piesei se face cu ajutorul unor indici tehnico-economici
absoluti sau relativi, cum sunt : masa piesei finite, gradul de
unificare al elementelor constructive.
Calculul
masei piesei finite :
O modalitate
de calcul a masei piesei este estimarea acesteia prin calculul volumului
piesei
si inmultirea acestuia cu densitatea materialului. Pentru calculul
volumului piesei, se descompune piesa in corpuri cu forme geometrice simple,
iar volumele acestora se aduna sau se scad, dupa caz.
m = Vt·
[g ]
unde:
m - masa piesei ;
Vt -
volumul total al piesei , [mm3 ]
- densitatea materialului ,[
g/cm3]
V=
I [mm3]
V1=
273.258 [mm3] V2=
72.006 [mm3]
V3=
36.543 [mm3]
V4=
35.068[mm3]
V5=
1.331 [mm3]
V6=
1.928 [mm3]
VTOTAL=(V1+V2)-(V3+V4+V5+V6)=270,394
[cm3]
m=270,394×7,86=2125,296g =2,125
[kg]
masa
piesei=2,125 [kg]
Pentru
piesa data se obtine un volum de 270,394 [cm3], iar prin
considerarea unei densitati de 7,86 [g/cm3], obtinem
o masa a piesei de 2,125 [kg]. Reiese ca piesa nu ridica
probleme in procesul tehnologic, facand parte din categoria pieselor mici.
Gradul de unificare a
elementelor constructive
Tipurile de elemente
constructive din cadrul piesei (conform datelor din tabel 1.1), sunt:
suprafete cilindrice
interioare;
suprafete cilindrice
exterioare;
gauri netede;
gauri filetate;
canale circulare
exterioare;
caneluri;
suprafete plane ;
Pentru fiecare tip de elemenet geometric, se inventariaza
numarul elementelor cu dimensiuni diferite - ed si
numarul total al elementelor - et, apoi se calculeaza
gradul de unificare constructiva, le tabel nr. 1.8.
Tabelul nr.1.8.
Gradul de unificare a
elementelor constructive
Tipul elementului constructiv
|
Codul suprafetelor / nr.
total elemente, et
|
Codul suprafetelor
/nr. elemente cu dimensiuni
diferite , ed
|
Gradul de unificare
constructiva
le = ed / et
|
Suprafete
plane-frontale
|
S1,S6,S8,S17/4
|
S1,S6,S8,S17/4
|
|
Suprafete
cilindrice exterioare
|
S4,S7/2
|
S4,S7/2
|
|
Suprafete
cilindrice interioare
|
S2,S9,S12,S16/4
|
S2,S9,S12,S16/4
|
|
Gauri
filetate
|
S13/1
|
S13/1
|
|
Caneluri
|
S10/1
|
S10/1
|
|
Canale
circulare
interioare
|
S11/1
|
S11/1
|
|
Tesituri
|
S3,S5,S14,S15/4
|
S3,S15/2
|
|
Se constata ca
gradul de unificare constructiva al razelor si tesiturilor, le<1, acest
lucru indica o buna tehnologicitate constructiva a piesei.
In schimb, restul
suprafetelor au gradul de unificare constructiva le ( toate dimensiunile suprafetelor sunt diferite intre ele).Acest lucru
arata o tehnologicitate constructiva minima a piesei.
Din punct de vedere al concordantei formei constructive a
produsului cu particularitatile diferitelor metode si procedee
de fabricare se poate mentiona :
profilul exterior se
poate realiza prin strunjire;
rectificarile
profilului exterior se pot executa usor;
gaurile sunt
accesibile, nu ridica probleme de gaurire;
In concluzie, avand in vedere cele expuse mai sus piesa prezinta
o buna tehnologicitate, neridicand probleme deosebite pentru
executie.
Tabel nr.1.9
Gruparea suparafetelor pe
tipuri de suprafete si procedee aplicabile acestora
Tip
suprafata
|
Nr.(cod)
suprafata
|
Procedee
de prelucrare aplicabile tipului de suprafata
|
Observatii
privind respectarea conditiilor de tehnologicitate
|
Cilindrica
exterioara
|
S4
|
Strunjire
de degrosare
|
Posibil
de realizat
|
S7
|
Strunjire
de degrosare,
Strunjire
de finisare, rectificare
|
Cilindrice
interioare
|
S2
|
Adancire
|
Posibil
de realizat
|
S9,S16
|
Strunjire
de degrosare
|
S12
|
Gaurire
|
Plan
frontale
|
S1,
S6,S8,S17
|
Strunjire
de degrosare
|
Posibil
de realizat
|
Conica(tesitura)
|
S3,
S5,S14,S15
|
Strunjire
de degrosare
|
Posibil
de realizat
|
Complexa(canelura)
|
S10
|
Brosare
de degrosare,
Brosare
de finisare
|
Posibil
de realizat
|
Complexa(canal
circular interior)
|
S11
|
Strunjire
de degrosare
|
Posibil
de realizat
|
Elicoidala
(filet)
|
S13
|
Filetare
|
Posibil
de realizat
|
2.
Proiectarea semifabricatului
2.1
Stabilirea metodelor si procedeelor de obtinere semifabricatului
Variantele
semifabricatului pentru piesa data prin proiect:
semifabricat laminat ;
semifabricat forjat liber pe ciocan de forjat.
O
problema care influenteaza foarte mult tehnologia de fabricatie
pentru un reper este alegerea variantei optime de semifabricat.
Semifabricatul
trebuie sa aiba o forma cat mai apropiata de forma piesei
finale pentru a necesita cat mai putine prelucrari, deci un consum
cat mai redus de material si energie.
Alegerea semifabricatului
optim consta in verificarea umatoarelor aspecte tehnico-economice:
felul semifabricatelor
corespunzatoare tehnic pentru piesa;
gradul de
apropiere al acestor semifabricate de piesa;
costul fiecarui semifabricat
tehnic posibil pentru piesa si alegerea semifabricatului cu cost minim.
Laminarea
Folosirea
semifabricatelor sub forma de bare laminate este indicata in cazul
productiei de unicate si serie mica.
Semifabricatele
sub forma de bare laminate se pot folosi si in cadrul productiei
de serie si masa, in special pentru piese din clasa arborilor,
atunci cand diferenta intre treptele arborilor este mica.
Intocmirea desenului
semifabricatului laminat, prezentat in figura 2.1 se face plecand de la desenul
de executie al piesei finite, la care se considera adaosurile de
prelucrare.

Figura
2.1-Semifabricat laminat
m = Vt·
ρ [g]
V=
I [mm3]
V=
I =
926.928 [mm3 ]
m=926.928 7,86=7285.35 g =7,28 [kg]
masa
semifabricatului laminat=7,28 [kg].
Matritarea
Semifabricatele
matritate prezinta avantaje insemnate in comparatie cu
semifabricatele forjate liber .La acest tip de semifabricate se
micsoreaza sau se exclud adaosurile tehnologice, inevitabile la piese
cu variatii bruste a formei, se reduc adaosurile de prelucrare, iar
tolerantele se micsoreaza de 34 ori.
Matritarea la cald permite obtinerea de semifabricate cu
precizie ridicata , practic pentru piese cu orice configuratie,
asigura o structura mai omogena a metalului, o calitate mai buna
a suprafetei.
Costul relativ ridicat al matritelor face ca acest procedeu sa
fie rentabil pentru un numar de piese corespunzator cel putin
productiei de serie mijlocie.
Matritarea constituie procedeul de prelucrare prin presiune a
metalelor si aliajelor prin care materialul in timpul deformarii
plastice se deformeaza simultan in intreg volumul, iar curgerea acestuia
este conditionata de forma si dimensiunile cavitatilor
sculelor (matrite). Dupa matritare urmeaza operatia de
debavurare, adica de inlaturare a surplusului de material colectat in
bavura.
Pentru micsorarea adaosului tehnologic se va urmari
geometria piesei prin matritare bilaterala, unde surplusul de
material se gaseste in planul de separatie. Canalul de
bavura poate prelua in anumite limite surplusul de material permitind
obtinerea de dimensiuni exacte, din semifabricate cu dimensiuni neexacte.
Stabilirea planului de separatie va tine seama de
posibilitatile de executie, extragerea piesei matritate si
de consumul de material in adaosul tehnologic, modul de curgere a materialului
in bavura.
Matritarea pe
ciocane
Este cel mai raspandit procedeu de deformare plastica la
cald folosindu-se in productia de serie sau masa pentru piese cu masa
pana la circa 1000 kg.
Matritarea
pe prese
Matritarea pe prese are urmatoarele avantaje in raport cu matritarea
pe ciocane:
precizie mai
ridicata datorita rigiditatii sporite a berbecului;
inclinatii mai
mici la peretii cavitatii datorita folosirii
extractoarelor;
posibilitatea
mecanizarii si automatizarii procesului;
productivitate
ridicata.
La intocmirea
desenului semifabricatului matritat trebuie realizate urmatoarele
faze succesive:
alegerea planului de
separatie;
stabilirea adaosurilor
de prelucrare;
stabilirea adaosurilor
tehnologice;
Intocmirea desenului semifabricatului matritat, prezentat in
figura 2.2 se face plecand de la desenul de executie al piesei finite, la
care se considera adaosurile de prelucrare si adaosurile tehnologice
(inclinari pentru scoaterea usoara a semifabricatului din cavitatea
matritei, raze de racordare pentru a elimina muchiile ascutite si
pentru a ajuta la curgerea materialului in cavitatile matritei.
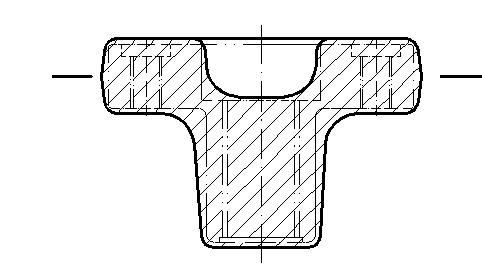
Figura
2.2-Schita semifabricatului obtinut pe masina de forjat orizontal
Adoptarea adaosurilor totale
de prelucrare
La semifabricatele matritate adaosurile sunt mai mici. H -este
dimensiunea maxima in inaltime masurata paralel cu
directia de matritare. L- dimensiunea maxima in lungime,
masurata perpendicular pe directia de matritare.
Clasele
de precizie la matritare sunt indicate pentru serii de productie mici
si mijlocii. Am ales clasa a II-a de precizie utilizata pentru
productia de serie mijlocie.
La
suprafetele matritate care se prelucreaza ulterior,
inclinatiile de matritare si razele de racordare se aplica la
cotele nominale marite cu valoarea adaosului de prelucrare respectiv.
Valorile adaosurilor de prelucrare stabilite de STAS 7670-66 pentru piesele din
otel matritate corespund pentru piese matritate care au
rugozitatea Ra = 2.5µm; daca suprafetele pieselor
matritate se prelucreaza mai fin, valorile adaosurilor se
majoreaza cu 0.25 mm pentru realizarea rugozitatii Ra=
3.212.5 µm si cu 0.5mm pentru suprafete cu Ra ≤1.6µm.
[.]
In tabelele
nr. 2.1 si 2.2 se prezinta adaosul de prelucrare pentru procedeele
considerate, iar in tabelele nr. 2.3 si 2.4 se prezinta valorile
razelor de racordare si valorile inclinatiilor de matritare.
Tabel nr. 2.1
Adaosurile
de prelucrare pentru laminare
Suprafata
|
Dimensiunile
suprafetei piesei
|
Adaos
total de prelucrare
|
Dimensiunea
suprafetei semifabricatului
|
H
|
|
|
|
D
|
|
|
|
Tabel nr. 2.2
Adaosurile de prelucrare pentru matritare
Suprafata
|
Dimensiunile
suprafetei piesei
|
Adaos
total de prelucrare
|
Dimensiunea
suprafetei semifabricatului
|
Abaterile
limita
|
Cota
finala
|
S4
|
H=25/L=118
|
|
|
L=
H= 
|
121.5
|
S6
|
H=25/L=118
|
|
|
L=
H= 
|
26,75 
|
S7
|
H=52/L=42
|
|
|
L=
H=
|
46
|
S8
|
H=77/L=42
|
|
|
L=
H=
|
79
|
S1
|
H=77/L=118
|
|
|
L=
H=
|
79
|
S17
|
H=22/L=46
|
|
|
L=
H=
|
43
|
S16
|
H=22/L=46
|
|
|
L=
H=
|
23,5
|
Valorile razelor de racordare sunt prezentate in tabelul 2.3.
Tabel nr. 2.3
Valorile razelor de racordare
Inaltimea
considerata hi, mm
|
Razele
de racordare, in mm pentru raportul
|
Peste
|
Pana
la
|
hi
/ bi < 2
|
r
|
R
|
|
|
|
|
|
|
|
|
Valorile inclinatiilor de matritare sunt prezentate in
tabelul 2.4.
Tabel 2.4
Valorile
inclinatiilor de matritare
Tipul utilajului de
matritat
|
Inclinatiile
de matritare maxime
|
M.f.v.
|
Suprafete
exterioare
|
Suprafete
interioare
|
|
|
V=
I [mm3]
V.1=
=387186.33 [mm3]
m=387186.33 7,86= 3043284,56 [g]=3,04 [kg]
2.
3 Adoptarea procedeului economic de realizare a semifabricatului
Alegerea
procedeului economic de realizare a semifabricatului se face pe baza unor
criterii dintre care:
a) Gradul de apropiere al semifabricatului de piesa se apreciaza pe baza volumului
relativ de material indepartat , determinat cu ajutorul relatiei urmatoare
- Vrmat =
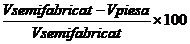
Pentru laminare:
Vrmat = 
Pentru matritare:
Vrmat
Tabel nr. 2.6
Gradul de apropiere al
semifabricatului de piesa
Volumul
de material indepartat %
|
Nota
|
|
|
|
|
|
|
|
|
|
|
b)Precizia semifabricatului se apreciaza in raport cu suprafata
de precizie cea mai mare a piesei(exceptand dantura). In acest scop s-a
utilizat tabele cu trepte de precizie si rugozitate medie economica
specifice procedelor de semifabricare.
Notele pentru
acest criteriu sunt comform tabelului urmator:
Tabel
nr.2.7
Precizia semifabricatului
Diferenta
intre treptele de precizie / rugozitate* semifabricat - piesa
|
|
|
|
|
|
Nota
acordata
|
|
|
|
|
|
*Diferenta dintre
treapta de precizie/rugozitate a semifabricatului si treapta de precizie/rugozitatea
cea mai mica a piesei.
c) Costurile
semifabricatului. Acest
criteriu se refera la costurile legate de procesul de obtinere a
semifabricatului.
Notele acordate
acestui criteriu sunt conform tabelului urmator:
Tabel nr.2.8
Costurile semifabricatului
Metoda
de obtinere a semifabricatului
|
Nota
acordata
|
Laminat
la cald
|
|
Tras
la rece
|
|
Matritat
|
1
- 3 (in functie de gradul de complexitate a semifabricatului)
|
Criteriile de analiza
sunt centralizate in tabelul 2.5.
Tabel nr. 2.5
Criteriile de analiza
Criteriul
|
Ponderea
criteriului
|
Tip
semifabricat
|
Note
pe tip semifabricat
|
Punctaj
pe tip semifabricat
|
Laminat
|
Matritat
|
Laminat
|
Matritat
|
Gradul
de apropiere al semifabricatului de piesa
|
|
Laminat
|
|
|
|
|
Matritat
|
Precizia
semifabricatului
|
|
Laminat
|
|
|
|
|
Matritat
|
Costul
semifabricatului
|
|
Laminat
|
|
|
|
|
Matritat
|
TOTAL PUNCTAJ PE SEMIFABRICAT
|
|
|
Conform analizei
efectuate rezulta ca semifabricatul economic este un semifabricat
matritat, deoarece are punctajul cel mai mare.
2
.4 Stabilirea tratamentelor termice primare necesare
Tratamentul termic
primar are ca scop imbunatatirea prelucrabilitatii
semifabricatului
(prin
aschiere) si de detensionare a acestuia.
Tabel nr.2.9
Tratamente termice
Marca
otelului
|
Recoacere
de inmuiere
|
SAU
|
Recoacere
intermediara
|
OLC45
|
Temp
0C
|
Mediul
de racire
|
Temp
0C
|
Mediul
de racire
|
|
cuptor
|
|
cuptor
|
2.5
Desenul de executie al semifabricatului
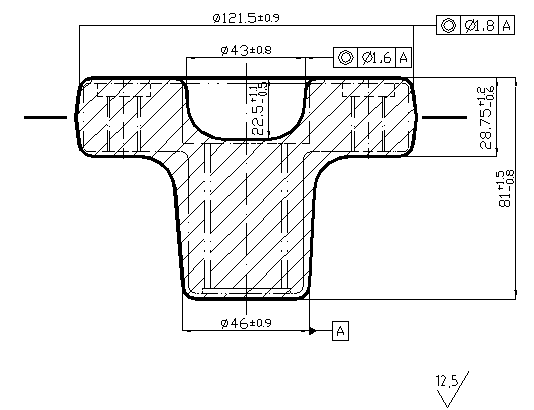
Figura 2.3- Desenul de
executie al semifabricatului
Nota: Toate
razele de racordare au valoarea R=12,5 [mm].
Toate
razele de rotunjire au valoarea r= 5 [mm]
Toate inclinatiile se executa la 7 o.
3.
Proiectarea variantelor preliminarii de proces tehnologic
3.1 Stabilirea metodelor si procedeelor de prelucrare a
suprafetelor semifabricatului
Piesa
care constituie obiectul temei, "Bucsa" face parte din grupa pieselor
de revolutie, iar materialul utilizat pentru realizarea acesteia este un
otel marca OLC 45.
Prelucrarea
bucselor sau in general a pieselor cu suprafete de revolutie
impune rezolvarea unor anumite probleme, cum ar fi realizarea
perpendicularitatii dintre suprafetele frontale si
suprafata cilindrica interioara luata ca baza de
referinta, insa se mai urmareste de asemenea si
obtinerea concentricitatii suprafetelor exterioare cu cele
interioare. In general, pentru confectionarea lor se folosesc drept
semifabricate barele laminate, materiale forjate si matritate.
Procesul
de executie al unei piese din clasa "bucse" este urmatorul:
- in prima
operatie se prelucreaza suprafetele frontale, cilindrice
exterioare si interioare posibil de prelucrat dintr-o prindere prin
strunjire de degrosare si finisare;
- prelucrarea din
celalalta prindere a piesei prin strunjire de degrosare;
- executarea gaurilor
filetate pe masina de gaurit;
- tratament
termic;
- rectificarea
dintr-o parte a suprafetelor care necesita acest procedeu;
- control final.
Pentru fiecare suprafata Sk sau grup de suprafete se
stabilesc pe baza de considerente tehnico-economice diferite variante
tehnic acceptabile privind procedeele sau succesiunea de procedee necesare
obtinerii preciziei dimensionale si a rugozitatii
suprafetei respective.
Metodele si procedeele de prelucrare a
suprafetelor sunt prezentate in tabelul nr.3.1.
Tabel nr. 3.1
Stabilirea etapelor de
prelucrare
Sk
|
Forma/Caracteristici
geometrice
prescrise
|
Varianta
de succesiune
|
Nr.
etape de prel.
|
Succesiunea
de prelucrari
|
Etapa
1
|
Etapa
2
|
Etapa
3
|
S4
|
Cilindricaexterioara ,
T11
(IT = 220μm),
Ra
= 6.3μm
|
I
|
|
Str.
degrosare
T11
(IT =220),
Ra=6,3
μm
|
|
|
S7
|
Cilindrica
exterioara

T6
(IT = 16μm) , Ra =0.8μm
|
I
|
|
Str.
degrosare
T
12(IT=250),
Ra
= 6,3 μm
|
Str.
finisare
T9
(IT=62), Ra=1,6 μm
|
Rectificare
T
6(IT = 16), Ra = 0,8 μm
|
S2
|
Cilindrica
interioara
T13(IT
= 330μm),
Ra
= 1.6μm
|
I
|
|
Adancire
T13
(IT = 330),
Ra=6,3
μm
|
|
|
S12
|
Cilindrica
interioara(Gaura) 
T
13 (IT = 220μm),
Ra
= 6,3 μm
|
I
|
|
Gaurire
T13(
IT=220)
Ra=6,3 μm
|
|
|
S9
|
Cilindrica
interioara
T
13 ( IT = 330μm),
Ra
= 6,3μm
|
I
|
|
Gaurire
T13
(IT = 270μm),
Ra
= 6,3μm
|
Gaurire
T13
(IT = 330μm),
Ra
= 6,3μm
|
Str.
degrosareT13 (IT =330μm),
Ra
= 6,3μm
|
S16
|
Cilindrica
interioara ,
T13 (IT = 390μm )
Ra
= 6,3 μm
|
I
|
|
Str.
degrosare
T13(IT
= 390 μm),
Ra=6,3
μm
|
|
|
S1
|
Plan
frontala
77/
T13
(IT = 460μm )
Ra
= 6,3 μm
|
I
|
|
Str.
degrosare
T13(IT
= 460 μm),
Ra=6,3
μm
|
|
|
S6
|
Plan
frontala
25/ /
T13
(IT = 330μm ) ,
Ra
= 6,3 μm
|
I
|
|
Str.
degrosare
T13(IT
= 330 μm),
Ra=6,3
μm
|
|
|
S8
|
Plan
frontala 77/
T13
(IT = 460μm ) ,
Ra
= 6,3μm
|
I
|
|
Str.
degrosare
T13
(IT =460μm ),
Ra=6,3
μm
|
|
|
S17
|
Plan
frontala 22 / / ,
T13(
IT=330) ,Ra=6,3 μm
|
I
|
|
Str.
degrosare
T13
(IT = 330)
Ra=6,3
μm
|
|
|
S3,
S5,S14
|
Conica
( tesitura )
1
x 45˚,T13( IT = 140μm) , Ra = 6,3μm
|
I
|
|
Str.
de degrosare
T13
(IT =140),
Ra=6,3
μm
|
|
|
S15
|
Conica
( tesitura )
0,5
x45 ˚ ,T13 (IT = 140μm), Ra = 6,3μm
|
I
|
|
Str.
de degrosare
T13
(IT =140),
Ra=6,3
μm
|
|
|
S11
|
Complexa(canal
circular interior) 2/1/
T13
(IT = 140 μm ) ,
Ra
= 6,3 μm
|
I
|
|
Str.
degrosare
T13(IT
= 140),
Ra=6,3
|
|
|
S10
|
Complexa
(canelura) / /2
T=8
(IT = 51μm ),
Ra
= 1,6μm
|
I
|
|
Brosare
T8
(IT
= 51μm) ,
Ra
= 1,6μm
|
|
|
S13
|
Elicoidala
(filet) M12x1,25
T13
(IT = 270μm ),
Ra
= 6,3μm
|
I
|
|
Gaurire
la T13
(IT=220)
Ra=6,3 μm
|
Tesire
1 x
45˚,
T13(
IT =140μm)
Ra
= 6,3μm
|
Filetare
cu tarod T13(IT=270μm)
Ra=6,3 μm
|
Incadrarea piesei
intr-o familie si grup de piese, reguli de proiectare si
restrictii specifice
Analizand forma si dimensiunile piesei se
observa ca aceasta face parte din categoria pieselor de
revolutie . Din punct de
vedere al raportului intre lungime si diametru piesa se incadreaza in
bucsa scurta cu alezaj.
Principile utilizate in stabilirea
ordinii prelucrarii:
In primele operatii
ale procesului tehnologic trebuie sa se prelucreze acele suprafete
care vor servi ca baze tehnologice la prelucrarea celorlalte suprafete ale
piesei;
Se va urmari
suprapunerea bazelor tehnologice cu cele de cotare in special la realizarea
conditiilor tehnice impuse in desenul de executie;
Succesiunea operatiilor
trebuie astfel stabilita incat sa se mentina pe cat posibil
aceleasi baze tehnologice la majoritatea operatiilor de prelucrare;
Daca baza de
cotare nu coincide cu baza tehnologica, este indicat ca in operatia
urmatoare sa se prelucreze baza de cotare;
Operatiile de degrosare,
in timpul carora se indeparteaza cea mai mare parte a adaosului de
prelucrare se efectueaza la inceputul procesului tehnologic;
La piesele prelucrate
din semifabricate turnate care au tensiuni interne prelucrarea de degrosare
trebuie separata in timp de cea de finisare pentru ca in intervalul dintre
ele sa se realizeze o detensionare naturala astfel incat la sfarsitul
procesului tehnologic de prelucrare tensiunile interne sa fie eliminate
complet;
Suprafetele cu
rugozitate mica si precizie ridicata se finiseaza in ultimele
operatii de prelucrare, pentru a se evita deteriorarea acestora in cursul
altor prelucrari sau al transportului pieselor la diferitele locuri de
munca;
Executarea gaurilor,
filetelor se recomanda a se realiza la sfarsitul procesului
tehnologic, in scopul evitarii deteriorarii in timpul altor prelucrari;
Se va urmari
stabilirea rationala a operatiilor de control tehnic prin
introducerea unui control tehnic intermediar dupa etapele importante de
prelucrare, degrosare, finisare, precum si inainte de executia
operatiilor costisitoare sau de precizie ridicata;
Tipuri de
restrictii (conditionari) ce impun succesiunea
operatiilor/fazelor unui proces tehnologic:
a) legaturile
dimensionale intre suprafete
daca intre doua
suprafete este impusa o toleranta de pozitie
relativa stransa, cele doua suprafete trebuie executate in
aceeasi operatie;
daca intre doua
suprafete exista o conditie de pozitie relativa, mai
intai se prelucreaza suprafata baza de referinta;
intre doua
suprafete, se prelucreaza mai intai cea care are precizia
dimensionala mai ridicata.
b) asocierile
geometrice si/sau tehnologice intre suprafete
sunt asociate geometric
mai multe suprafete realizate cu aceeasi scula aschietoare.
sunt asociate tehnologic
suprafete de acelasi tip, repartizate regulat ce pot fi realizate cu
aceeasi scula aschietoare, in aceeasi
operatie/faza.
sunt asociate tehnologic
suprafetele ce trebuie realizate din aceeasi orientare si fixare
a semifabricatului (datorita legaturilor dimensionale impuse)
c) succesiunea
etapelor de prelucrare
alegerea numarului de
etape de prelucrare depinde de precizia dimensionala si de
rugozitatea impusa suprafetei de prelucrat.
Daca o
suprafata necesita mai multe etape de prelucrare, succesiunea
acestora trebuie sa fie: degrosare,
semifinisare, finisare, superfinisare.
d) utilizarea
sculei aschietoare
in legatura cu
scula aschietoare utilizata pentru prelucrare, doua aspecte
importante trebuie luate in considerare: uzura si deformatiile
provocate in sistemul tehnologic.
deformatiile in
sistemul tehnologic sunt provocate de vibratiile introduse de lungimile
mari in consola ale sculelor, de razele la varf mari si necorelate cu
valoarea avansului, de aschierea discontinua sau cu socuri.
e) locul
operatiei de tratament termic
necesitatea unei
operatii de tratament termic aplicat semifabricatului impune o ordine
anumita operatiilor de prelucrare mecanica, functie de
tipul tratamentului termic (in volum sau de suprafata), de materialul
semifabricatului si de materialul partii active a sculei.
Restrictiile
specifice reperului analizat sunt prezentate in tabelul nr.3.2.
Tabel nr.3.2
Restrictii specifice
piesei
Desenul
de executie al piesei
|
Conditia
impusa
|
Ordinea
prelucrarilor
|
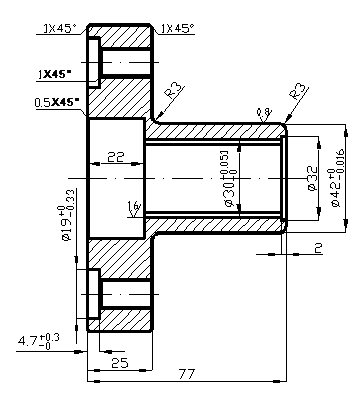
|
Pe
desenul de executie nu exista abateri de forma sau de pozitie acestea
se subinteleg.
Perpendicularitatea
suprafetelor plan-frontale fata de axa piesei.
Asocierea
tehnologica a suprafetelor de acelasi tip,dispuse regulat,
care se executa cu aceeasi scula (suprafete cilindrice
exterioare, suprafete cilindrice interioare)
Succesiunea
etapelor de prelucrare
|
Suprafetele
se prelucreaza in aceeasi orientare si fixare a piesei
(universal cu trei bacuri).
La
piesele suficient de rigide etapele de finisare pot fi realizate imediat
dupa etapele de degrosare
|
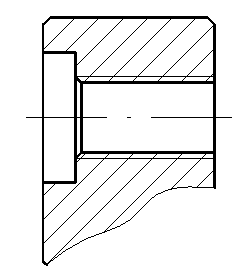
|
Protejarea
varfului sculei de gaurit.
Ghidarea
sculei de
adancit.
|
Gaurire
Adancire
Tesire
Filetare
|
3.3 Stabilirea
continutului si succesiunii operatiilor procesului tehnologic in
doua variante
Itinerarul tehnologic se stabileste in doua variante avand
in vedere urmatoarele:
principiile si
restrictiile tehnico-economice generale privind proiectarea procesului
tehnologic:
succesiunea etapelor
procesului tehnologic.
In structura preliminara
a procesului tehnologic sunt incluse operatiile de prelucrare si
cele de tratament termic.
Pentru operatiile de
prelucrare sunt indicate:
nr de ordine si
denumirea operatiei
schita operatiei
, in care sunt precizate
piesa in pozitie
de prelucrat, avand suprafetele care se prelucreaza desenate cu linie
groasa;
orientarea si
fixarea piesei;
sculele reprezentate la
sfarsitul curselor de lucru;
miscarile de
generare;
rugozitatea
suprafetei prelucrate.
tipul
masinii-unelte folosite, al sculelor si al SDV-urilor.
Tabel
nr. 3.2
Varianta
1
Denumirea si schita
operatiei
|
Echipament tehnologic
|
Operatia
10 : Matritare
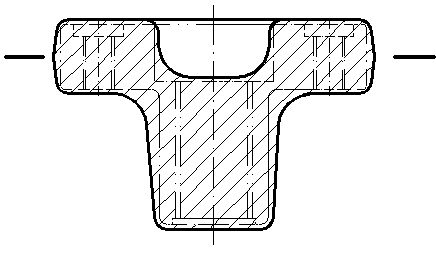
Dupa
realizarea operatiei de matritare, se executa debavurarea piesei,deoarece
orientarea piesei se va face pe diametrul ce contine planul de
separatie.
|
Masina de forjat verticala
|
Operatie 10: Strunjire
I
C1(T01):S8(D);S7(D);
S6(D); S5(D);
C2(T02):S8(D);
C3(T03):S9(D);
C4(T04):S9(D);
C5(T05): S9 (D);
C6 (T06): S11(D);
C7(T07): S7(F);
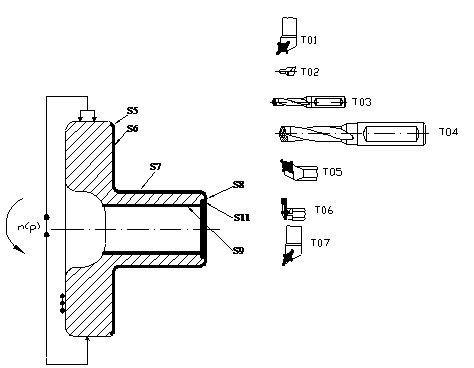
|
Masina
unealta: Strung cu CN GT400
Scule:Cutite de strunjit cu
placute din CM
T01 - cutit de strunjit
exterior(degrosare)
T02 - burghiu de centruit
T03 - burghiu de gaurit la Ĝ12,7
T04 - burghiu de gaurit la
Ĝ20
T05 - cutit de strunjit
interior (degrosare)
T06- cutit de prelucrare
canal circular interior
T07 - cutit de strunjit
exterior (finisare)
Dispozitiv:Universal cu 3 bacuri;
Verificator:
Subler
cu Vdiv=0,1 [mm], STAS 2301/ 87;
Calibre
;
Frecventa de masurare
1/10 piese
|
Operatia 20:
Strunjire II
C1(T01): S1(D), S3 (D),
S4(D);
C2(T02): S17(D), S16(D),
S(15);
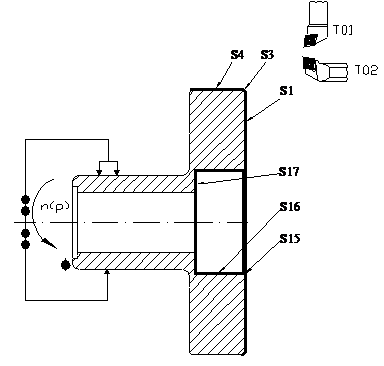
|
Masina
unealta: Strung cu CN GT400
Scule:Cutite de strunjit cu
placute din CM
T01 - cutit de strunjit
exterior(degrosare);
T02 - cutit de strunjit
interior(degrosare);
Dispozitiv:Universal cu 3 bacuri;
Verificator:
Subler
cu Vdiv=0,1 [mm], STAS 2301/ 87;
Calibru
tampon;
Frecventa de masurare 1/10 piese
|
Operatia 30 :
Gaurire, Adancire, Tesire, Filetare
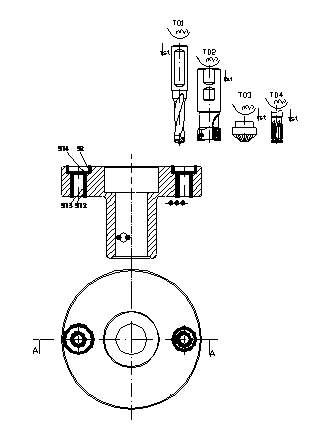
|
Masina unealta:Masina de
gaurit si filetat GPR 45 cu cap revolver
Scule:Burghiu , Adancitor ,
Adancitor conic si Tarod;
Dispozitiv: Dispozitiv special de
gaurit
Bolt si reazem pt
suprafete plane
Verificator:
Calibre;
Frecventa de
masurare 1/10 piese
|
Operatia 40:Brosare
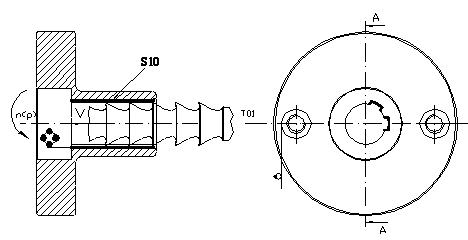
|
Masina unealta:Masina de brosat
7A520
Dipozitiv: Dispozitiv de
brosat
Scule: Brosa din p3
Verificator:
Calibru tampon;
Frecventa de
masurare 1/10 piese
|
Operatia 50 -
Control tehnic intermediar
Fara
schita
|
Masa de control
Se controleaza
cotele :
Gaurile
de ;
Filete
M12
|
Operatia 60 - Tratament
termic
Fara
schita
|
Masina unealta :Instalatie
tratament termic;
Calire - revenire
|
Operatia 70 - Rectificare
cilindrica exterioara
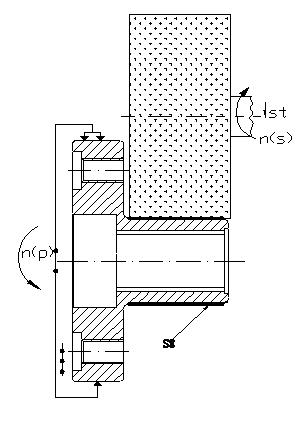
|
Masina unealta Masina de
rectificat WMW 500
Scula:Corp abraziv cilindric
plan
Universal cu
3 bacuri
Reazem pt
suprafete plane
Verificator:
Micrometru
cu
Vdiv =0,001 mm, STAS
2303/88
Rugozimetru;
Calibre
potcoava
Frecventa de
masurare 1/10 piese
|
Operatia 80
-Control final
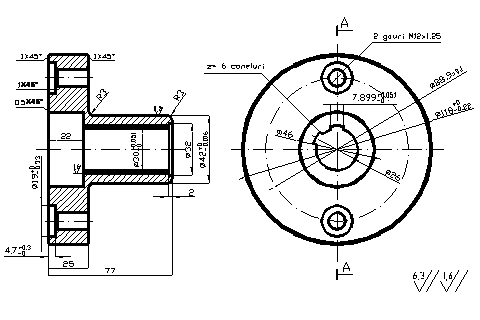
|
Masina unelta:Banc de masura
si control
Se controleaza
cotele:
Diametrele
exterioare la , ;
Alezajul
la ;
Rugozitatea
suprafetelor de , ;
Verificator:
Calibre;
Micrometru
cu Vdiv=0,01 mm, STAS 2303/ 88;
Rugozimetru
|
Tabel nr.3.3
Varianta 2
Numar operatie
, denumire ,schita
|
Echipament tehnologic
|
Operatia 0 -
Debavurare
Idem varianta I
|
Idem varianta I
|
Operatia 10 -
Matritare
Idem varianta I
|
Idem varianta I
|
Operatia 20- Strunjire
I
Idem varianta I
|
Idem varianta I
|
Operatia 30 -
Strunjire II
Idem varianta I
|
Idem varianta I
|
Operatia 40
- Gaurire Ĝ 10.2
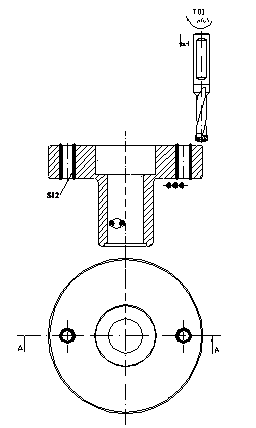
|
Masina
unealta:Masina de gaurit G25
Scule: Burghiu;
Dispozitiv:Dispozitiv special de
gaurit
Bolt cilindric
scurt;
Verificator:
Calibru
;
Frecventa de
masurare 1/10 piese
|
Operatia 50
- Adancire
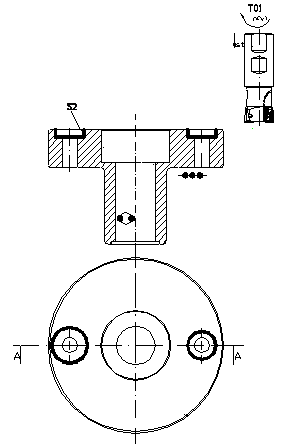
|
Masina
unealta:Masina de gaurit G25
Scule: Adancitor;
Dispozitiv:Dispozitiv special de
gaurit
Bolt cilindric
scurt;
Verificator:
Calibru
;
Frecventa de
masurare 1/10 piese
|
Operatia 60
-Tesire

|
Masina
unealta:Masina de gaurit G25
Scule: Adancitor conic;
Dispozitiv:Dispozitiv special de
gaurit
Bolt cilindric
scurt;
Verificator:
Calibru;
Frecventa de
masurare 1/10 piese
|
Operatia 70 - Filetare
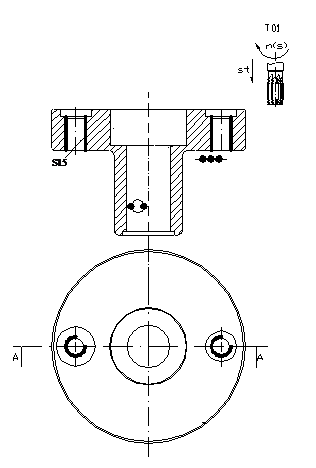
|
Masina unealta:
Masina de gaurit G25
Scule: Tarod;
Dispozitiv:Dispozitiv special de
gaurit
Bolt cilindric
scurt;
Verificator:
Calibru
;
Frecventa de
masurare 1/10 piese
|
Operatia 80 -
Brosare
Idem varianta I
|
Idem varianta I
|
Operatia 90 -
Rectificare cilindrica exterioara
Idem varianta I
|
Idem varinata I
|
Operatia 100 -
Control final
Idem varianta I
|
Idem varianta I
|
4.Proiectarea primei variante de proces tehnologic
Unul dintre cele doua procese tehnologice de prelucrare a
piesei, stabilite in capitolul precedent, va fi proiectat in detaliu
(vor fi stabilite toate elementele necesare punerii in practica a
tehnologiei).
4.1 Stabilirea adaosurilor de prelucrare si a
dimensiunilor intermediare
Obiectivele acestei etape de proiectare este de a stabili adaosurile
necesare prelucrarilor suprafetelor piesei si calculul
dimensiunilor intermediare ale acestor suprafete.
Tabel nr. 4.1
Dimensiuni intermediare ale suprafetelor
Supraf.
|
Denumire
procedeu
|
T
[mm]
|
As/Ai
[mm]
|
Adaos
total/
intermediar
[mm]
|
Dimensiunea
nominala
[mm]
|
Dimensiunea
prescrisa
[mm]
|
S7
Φ42
|
Matritare
|
|
|
|
|
|
Strunjire
degrosare
|
|

|
|
|
Φ
43,04
|
Strunjire
finisare
|
|

|
|
|
Φ42,3
|
Rectificare
|
|

|
|
|
Φ42
|
S4
Φ118
|
Matritare
|
|
|
|
|
|
Strunjire
degrosare
|
|

|
|
|
Φ118
|
S10
|
Gaurire
Φ12.7
|
|

|
|
|
Φ12,7
|
Gaurire
Φ20
|
|

|
|
|
Φ20
|
Strunjire
degrosare
|
|

|
|
|
Φ26
|
S17
Φ46
|
Matritare
|
|
|
|
|
|
Strunjire
degrosare
|
|

|
|
|
Φ46
|
S1
|
Matritare
|
|

|
|
|
79
|
Strunjire
degrosare
|
|

|
|
|
77
|
S8
|
Matritare
|
|

|
|
|
79
|
Strunjire
degrosare
|
|

|
|
|
77
|
S6
|
Matritare
|
|

|
|
|
26.75
|
Strunjire
degrosare
|
|

|
|
|
25
|
S16
|
Matritare
|
|
|
|
|
|
Strunjire
degrosare
|
|

|
|
|
22
|
4.2
Proiectarea operatiei numarul 20 : Strunjire II
Obiectivul acestei etape este de a proiecta fiecare operatie a
procesului tehnologic considerat.
4.2.1
Intocmirea schitei operatiei
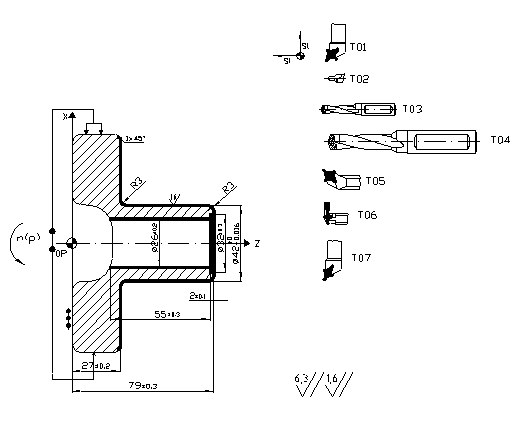
4.2.2 Precizarea fazelor de lucru ale operatiei
A.
Orientarea si
fixarea piesei in dispozitiv;
1. Strunjire de degrosare contur exterior;
B. Indexare turela;
2. Centruire la Ĝ2;
C.
Indexare turela;
3. Gaurire la Ĝ12,7
D. Indexare turela;
4. Gaurire la Ĝ20;
E.
Indexare turela;
6. Strunjire de degrosare cilindrica
interioara la cota Ĝ26;
F. Indexare turela;
5. Strunjire canal circular interior la cota 2/2/ Ĝ 32;
G. Indexare turela
7. Strunjire de finisare cilindrica exterioara
la cota Ĝ42,305
H. Desprins piesa din dispozitiv.
Tabel nr. 4.2
Schita
operatiei
|
Punctele
caracteristice/ coordonatele
|
X
|
Z
|
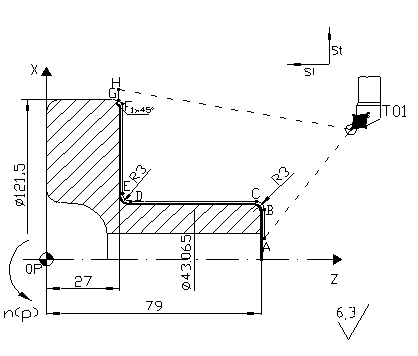
|
A
|
|
|
B
|
|
|
C
|
|
|
D
|
|
|
E
|
|
|
F
|
|
|
G
|
|
|
H
|
|
|
N01
G36 XZ
T01 01 M03 M06
N02
G00 G96 G38 X15 Z81 S236 F0.410 R2
N03
G01 Z81
N04
X36.065 Z78
N05
G03 X 43.065 Z78 I 78 K 40.065
N06
G01 Z30
N07
G02 X49.065 Z27 I49.065 K30
N08
G01 X119,5
N09
X121,5 Z26
N10
G00 X125 Z 81
|
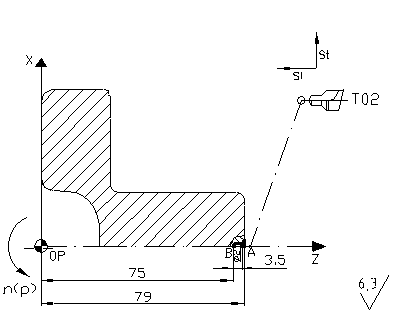
|
A
|
|
|
B
|
|
|
N11
G36 XZ T02 02 M06
N12
G00 G96 G27 X0 Z81 S12 F001
N13
G01 Z75
N14
Z81
|
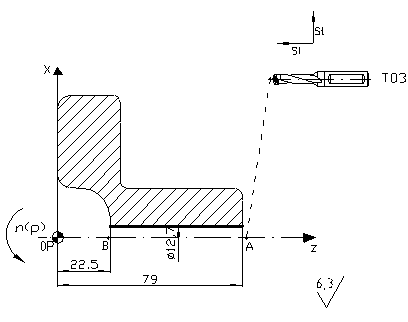
|
A
|
|
|
B
|
|
|
N15
G36 XZ
T03 03 M06
N16
G00 G96 G27 X0 Z81
N17
G01 Z20
N18
G00 Z81
|
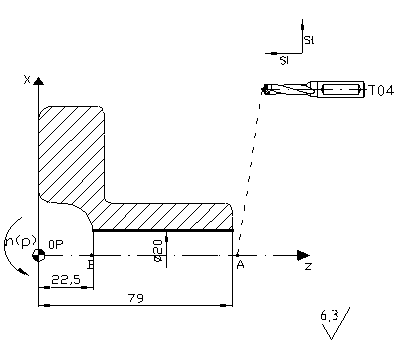
|
A
|
|
|
B
|
|
|
N19
G36 XZ T04 04 M06
N20
G00 G96 G27 X0 Z81
N21
G01 Z20
N22
G00 Z81
|
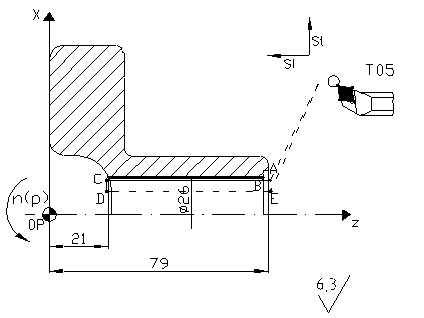
|
A
|
|
|
B
|
|
|
C
|
|
|
D
|
|
|
E
|
|
|
N23
G36 XZ T05 05 M06
N24
G00 G96 X26 Z81 S236 F0.410 R2
N25
G01 Z77
N26
Z20
N27
G00 X15
N28
Z81
|
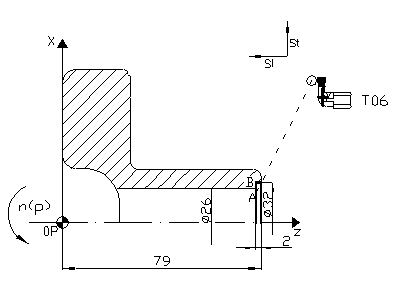
|
A
|
|
|
B
|
|
|
N29
G36 XZ
T06 06 M06
N30
G00 G96 X 23 Z77 S130 F 0.4
N31
G01 X32
N32
G00 X23
|
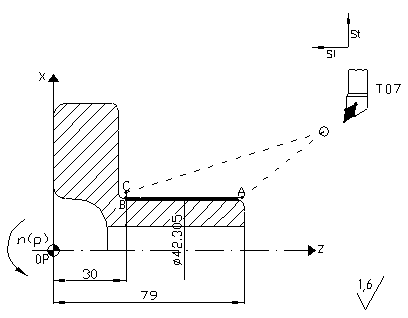
|
A
|
|
|
B
|
|
|
C
|
|
|
N33
G36 XZ T07 07 M06
N34
G00 G96 X42.305 Z79
N36
G01 Z30
N37
X45
N38
G00 Z81
|
| | | | | | |
4.2.3Stabilirea principalelor caracteristici ale
elementelor sistemului
tehnologic
Masina-unealta:
GT 400 Strung cu
comanda numerica
Caracteristicile tehnologice:
Zona de lucru:
- diametrul de
trecere pe deasupra batiulu . . . . . ..mm . . . ..470
- diametrul de
trecere pe deasupra saniei transversale . ..mm . . 310
- distanta
intre varfuri . . . . . . . . . . . . . ..mm . . ..755
- cursa pe axa X-Z . . . . . . . . . . . . . . .mm . .230-650
Antrenarea principala:
- Conul arborelui
principal . . . . . . . . . DIN 55026.A2-6''
- Diametrul
interior de rulare . . . . . . . . . mm . . . . .110
- Puterea motorului
100% ED . . . . . . . . kw . . . . .15
- Cuplajul
maxim . . . . . . . . . . . . . Nm . . . 293
- Plaja de
viteze . . . . . . . . . . . . . . .m/min . 20-4000
Papusa mobila:
- Diametrul
arborelui . . . . . . . . . . . .mm . . . .95-135
- Conul arborelui
. . . . . . . . . . . . . mm . . . .5
- Forta de impingere a arborelui . . . . . . . . N . . . . . 9200
Turela:
- Nr. de scule
fixe/rotative . . . . . . . . . . . . . . . .12/12
- Diametrul cozii
sculei VDI . . . . . . . . . mm . . . . . .40
- Puterea sculei
rotative . . . . . . . . . . . kw . . . . . .4
Caracteristicile generale:
- Greutatea
. . . . . . . . . . . . . . . . .kg . . . . . ..5000
- Puterea . . . . . . . . . . . . . . . . . KVA . . . . . .3
Dispozitiv de
orientare si fixare a piesei: universal cu trei bacuri;
Sculele de
prelucrare sunt: cutite
normale de prelucrare prin aschiere, formate din suport si
placute schimbabile din carburi metalice, specifice
prelucrarilor ce se executa (degrosare/finisare suprafete
exterioare si interioare);
Se va utiliza pentru alegerea sculelor de strunjit, catalogul firmei
SANDVIK COROMANT.[.]
Pentru strunjirea cilindrica exterioara si plana,
se va utiliza cutitul T01, si avand in vedere de asemenea
adaosul de prelucrare este recomandat sa se utilizeze sistemul de prindere
T-MAXP (placute cu geometrie negativa) (figura 4.1), sistemul
CoroTurn RC impunand o sectiune minima a suportului de 20x20 si
nu poate fi montat in turela.Se va alege o placuta tip C80˚
,adica o placuta rombica cu unghiul la varf de
80˚(figura 4.2) si un suport de tip PCLNL ce poate lucra atat cu
avans longitudinal cat si cu avans transversal, cu un unghi de atac de
95˚ cu placuta tip C (figura 4.3).
Se va alege suportul tip PCLNL 16 16 H 09 care permite realizarea unei
adancimi de aschiere ap= 3.5 mm ceea ce este suficient din
punct de vedere al adaosului de prelucrare la degrosare.
Semnificatia codului suportului sculei de strunjit este
prezentata in tabelul 4.3.
Tabel nr.4.3
Semificatia codului
suportului
Notatia
|
Semnificatia
|
P
|
Fixare
pe interior
|
C
|
Placuta
rombica cu unghiul la varf de 80˚
|
L
|
Unghiul
de atac Kr= 95˚
|
N
|
Unghiul
de asezare constructive al placutei = 0˚
|
L
|
Directia
de aschiere, spre stanga
|
|
Inaltimea
suportului, 16 mm
|
|
Latimea
suportului, 16 mm
|
H
|
Lungimea
suportului, 100mm
|
|
Dimensiunea
caracteristica a placutei, 9 mm
|
Se va alege tipul placutei si nuanta de carbura:
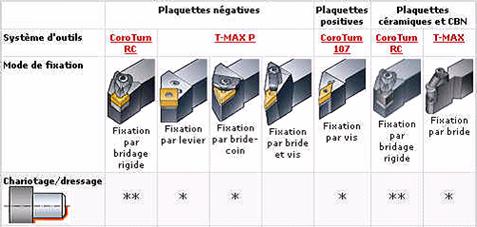
Figura 4.1 - sisteme de prindere a placutelor
in suport
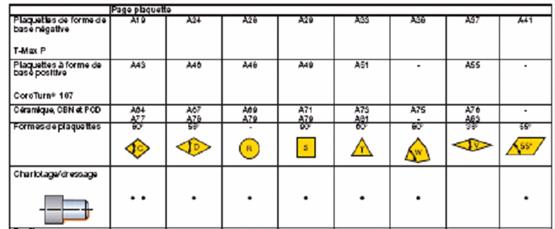
Figura4.2
- Tipurile de placute in functie de forma lor
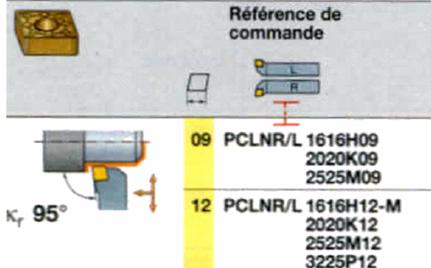
Figura 4.3 - Tipul de suport in functie de
unghiul de atac Kr
si dimensiunea caracteristica a
placutei
Nuanta de carbura
recomandata este GC 4025(pag A382)[.].
Placuta
aleasa este CNMG 09 03 08-PR (pag A21)[].
Semnificatia
codului placutei este prezentata in tabelul 4.4.
Tabel nr.4.4
Semnificatia codului placutei
C
|
Forma
placutei, rombica cu unghiul la varf de 80°
|
N
|
Unghiul
de asezare constructive=0°
|
M
|
Clasa
de toleranta
|
G
|
Tipul
constructive: cu alezaj central si canale de fragmentare pe ambele
parti
|
|
Dimensiunea
caracteristica: 9.525 mm
|
|
Grosimea
placutei:3.180 mm
|
|
Raza
la varf:0.8 mm
|
P
|
Specificatia
constructorului ISO P
|
M
|
Specificatia
constructorului - degrosare
|
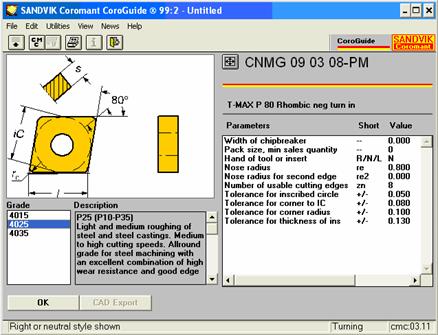
Figura4.4 - Tipul de placuta aleasa la
degrosare
Cutit T01
Placuta:
CNMG 09 03 08-PM, avand dimensiunea caracteristica de 9.525 mm si grosimea
placutei de 3.180 mm.
Suport : PCLNL
16 16 H 09, cu dimensiunea caracteristica a placutei de 9.525
mm.
Nuanta de
carbura a placutei: GC 4025.
Sistemul de
prindere: T-MAX P Lever
Cutit T02:
Burghiu de
centruire, forma A, STAS 1114/2-82, avand urmatoarele dimensiuni:
diametrul D = 3.15
mm;
lungimea totala L = 29.5 mm;
lungimea l = 1.3 mm.
Pentru
gaurire se utilizeaza un burghiu T03 de diametrul Ĝ12.7 de
tip R420.22-0127L20-41 cu avans longitudinal , cu 2 placute de tip LCMX 02
02 04C-53 1020.
T04 burghiu de diametru Ĝ20 cu suport de tip
R416.22-0127L20-41 cu avans longitudinal , cu 2 placute de tip LCMX 02 02
04C-53 1020.
Cutit
T05
Placuta: CNMG 09 03 08-PM
Suport: SCLCL 16 16 H 09
Nuanta de carbura: GC 4025.
Sistemul de prindere: T-MAX U Screw-fixare cu surub.
Cutit T06
Placuta : N123-E1 0200-0002-CM 1125 avand latimea
de 2 mm,unghiul de atac de 0°, raza la varf de 0.4 mm si lungimea
placutei de 19.2 mm.
Suport: RAG 150.23-50V-0476C;
Sistemul de prindere: CoroCut;
Nuanta de carbura: GC 1225.
Cutit T07
Placuta: : VNMG 16 04 04 - PF 1525
Suport: SVJBL 1616 H11
Nuanta de carbura: GC 4015
Sistemul de prindere: T-MAX P Lever
Verificator:
Calibru
4.2.4 Stabilirea metodei de reglare la dimensiune a sistemului
tehnologic
Metoda de reglare a sistemului tehnologic: se face cu piese de proba.
4.2.5 Determinarea
valorilor parametrilor regimului de lucru
Pentru burghiul de centruire T01:
avansul s = 0.01
mm/rot;
viteza v = 12 m/min.
Pentru burghiul T02, Ĝ12.7 :
Tabel 4.5 valorile parametrilor regimului de
aschiere pentru burghiul T02
Adancimea
de aschiere
t
[mm ]
|
Avansul
de
aschiere
s[mm/rot]
|
Viteza
de
aschiere
v[m/min]
|
Durabilitatea
T [mm]
|
Turatia
n[rot/min]
|
Forta
axiala
Fax
[N]
|
Nr.de
treceri i
|
Momentul
Mas
[Nmm]
|
Puterea
[KW]
|
|
|
|
|
|
|
|
|
|
Pentru burghiul T03, Ĝ20:
Tabel nr. 4.6
Valorile
parametrilor regimului de aschiere pentru burghiul T03
Adancimea
de
aschiere
t[
mm ]
|
Avansul
de
aschiere
s[mm/rot
|
Viteza
de
aschiere
v
[m/min]
|
Durabilitatea
T
[mm]
|
Turatia
n[rot/min]
|
Forta
axiala
Fax
[N]
|
Nr.de
treceri i
|
Momentul
Mas
[Nmm]
|
Puterea
[KW]
|
|
|
|
|
|
|
|
|
|
Tabel nr.
4.7
Valorile
regimului de aschiere pentru fiecare etapa in parte
Etapa
|
Caracteristicile
sculei
Sistemul
de prindere
|
Suprafata
|
D
[mm]
|
t
[mm]
|
L
[mm]
|
Ra
[μm]
|
tb
[min]
|
s
[mm/rot]
|
Vc
[m/min]
|
N
[rot/min]
|
P
KW
|
I
|
CNMG
09 03 08-PM
T-MAX
P,lever
|
S11
|
|
|
|
|
|
|
|
|
|
S9
|
|
|
|
|
|
|
|
|
|
S6
|
|
|
|
|
|
|
|
|
|
II
|
Placuta
: N123-E1 0200-0002-CM 1125
|
S14
|
|
|
|
|
|
|
|
|
|
III
|
CNMG
09 03 08-PM
T-MAX
U , Screw
|
S12
|
|
|
|
|
|
|
|
|
|
IV
|
VNMG
16 04 04 - PF 1525
T-
MAX P , Lever
|
S9
|
|
|
|
|
|
|
|
|
|
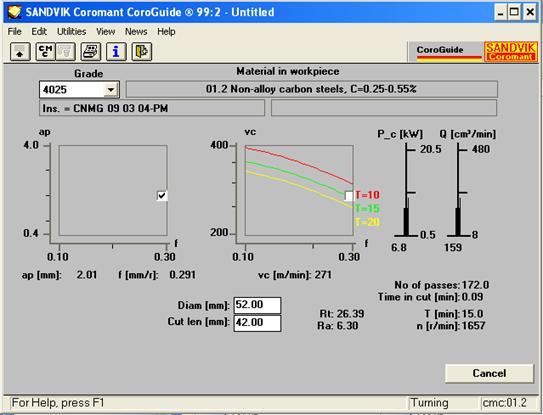
Figura 4.5- Regim de
aschiere
4.2.6 Stabilirea componentelor
ciclului de munca si determinarea normei de timp
Tabel
nr.4.8
Ciclograma operatiei
Denumire piesa
|
BUCSA
|
Nr. si denumire
operatie
|
10/Strunjire
| |
Material piesa
|
OLC 45
|
Masina-unealta
|
GT400
| |
Nr. crt.
|
Denumirea activitatii
|
S.D.V. - urile
utilizate
|
Regim de aschiere
|
Timpi [ cmin]
| |
v
|
f(s)
|
n
|
a(t)
|
i
|
vf
|
L
|
ta
|
tam
|
tb
|
tma
|
tf
|
|
Prindere
SF (din container)
|
Universal
cu 3 bacuri
Burghiu
de centruire, forma A, STAS 1114/2-82
Burghiu
Ĝ12.7
Burghiu
Ĝ20
Cutit
pentru degrosat exterior
Cutit
profilat
Cutit
de degrosat interior
Cutit
de finisat excterior
|
|
|
|
|
|
|
|
|
|
|
|
|
|
Orientare
- fixare SF in dispozitiv
|
|
|
|
|
|
|
|
|
|
|
|
| |
|
|
|
|
|
|
|
|
|
|
|
|
|
Pornire
ciclu de lucru automat
|
|
|
|
|
|
|
|
|
|
|
|
|
|
Deplasare
rapida a sculei T01
|
|
|
|
|
|
|
|
|
|
|
|
|
|
Strunjire
S11
|
|
|
|
|
|
|
|
|
|
|
|
|
|
Strunjire
S9
|
|
|
|
|
|
|
|
|
|
|
|
|
|
Strunjire
S6
|
|
|
|
|
|
|
|
|
|
|
|
|
|
Retragere
rapida scula
|
|
|
|
|
|
|
|
|
|
|
|
|
|
Indexare
turela
|
|
|
|
|
|
|
|
|
|
|
|
|
|
Deplasare
rapidaa a sculei T02
|
|
|
|
|
|
|
|
|
|
|
|
|
|
Centruire
|
|
|
|
|
|
|
|
|
|
|
|
|
|
Retragere
rapida scula
|
|
|
|
|
|
|
|
|
|
|
|
|
|
Indexare
turela
|
|
|
|
|
|
|
|
|
|
|
|
|
|
Deplasare
rapida a sculei T03
|
|
|
|
|
|
|
|
|
|
|
|
|
|
Gaurire
ĝ12,7
|
|
|
|
|
|
|
|
|
|
|
|
|
|
Retragere
rapida scula
|
|
|
|
|
|
|
|
|
|
|
|
|
|
Indexare
turela
|
|
|
|
|
|
|
|
|
|
|
|
|
|
Deplasare
rapida a sculei T04
|
|
|
|
|
|
|
|
|
|
|
|
|
|
Gaurire
ĝ20
|
|
|
|
|
|
|
|
|
|
|
|
|
|
Retragere
rapida scula
|
|
|
|
|
|
|
|
|
|
|
|
|
|
Indexare
turela
|
|
|
|
|
|
|
|
|
|
|
|
|
|
Deplasare
rapida a sculei T05
|
|
|
|
|
|
|
|
|
|
|
|
|
|
Strunjire
S14
|
|
|
|
|
|
|
|
|
|
|
|
|
|
Retragere
rapida scula
|
|
|
|
|
|
|
|
|
|
|
|
|
|
Indexare
turela
|
|
|
|
|
|
|
|
|
|
|
|
|
|
Deplasare
rapida a sculei T06
|
|
|
|
|
|
|
|
|
|
|
|
|
|
Strunjire
S12
|
|
|
|
|
|
|
|
|
|
|
|
|
|
Retragere
rapida scula
|
|
|
|
|
|
|
|
|
|
|
|
|
|
Indexare
turela
|
|
|
|
|
|
|
|
|
|
|
|
|
|
Deplasare
rapida a sculei T07
|
|
|
|
|
|
|
|
|
|
|
|
|
|
Strunjire
S9
|
|
|
|
|
|
|
|
|
|
|
|
|
|
Retragere
rapida scula
|
|
|
|
|
|
|
|
|
|
|
|
|
|
Desprinderea
piesei
|
|
|
|
|
|
|
|
|
|
|
|
|
|
Depozitarea
piesei in container
|
|
|
|
|
|
|
|
|
|
|
|
|
|
Curatarea
dispozitivului de aschii
|
|
|
|
|
|
|
|
|
|
|
|
|
|
Control
piesa (F = 1/10 piese)
|
|
|
|
|
|
|
|
|
|
|
|
| |
Ciclograma
operatiei
|
Total categorii de timp [cmin]
|
|
|
|
|
| |
tf
|
|
|
|
|
|
|
|
|
|
|
|
|
|
|
|
|
|
|
|
|
|
|
|
|
|
|
|
|
tam
|
|
|
|
|
|
|
|
|
|
|
|
|
|
|
|
|
|
|
|
|
|
|
|
|
|
|
|
Timp de pregatire-incheiere,
Tpi [min/lot] 15
|
tb
|
|
|
|
|
|
|
|
|
|
|
|
|
|
|
|
|
|
|
|
|
|
|
|
|
|
|
|
|
tma
|
|
|
|
|
|
|
|
|
|
|
|
|
|
|
|
|
|
|
|
|
|
|
|
|
|
|
|
Timp unitar, Tu
[min/buc] 2,55
|
ta
|
|
|
|
|
|
|
|
|
|
|
|
|
|
|
|
|
|
|
|
|
|
|
|
|
|
|
|
|
Scara
timpului [cmin]
|
Norma de timp, TN
[min/buc]
|
| |
|
|
| |
Numar
de piese pe lot [buc]
|
|
Durata executiei lotului de
piese, [min/lot]
|
|
Elemetele normei
de timp pe operatie sunt:
- timpul unitar
(care se consuma identic pentru realizarea unei piese) rezulta
din ciclograma operatiei: activitatile 1 - 35 se
realizeaza la fiecare piesa in parte (cumuleaza 2,4[cmin]), iar
activitatea 36, activitate de control se realizeaza o data la 10
piese (durata ce revine unei piese este de 150/10=15).
Se obtine Tu =255 [cmin/buc] =2,55 [min/buc].
- Norma de timp pe
operatie este:
TN = Tu + Tpi / N = 255+ 15/100 = 270
[cmin/buc] = 2,7[min/buc]
in care N reprezinta numarul de
piese din lot.
- Durata necesara
executarii lotului de piese, DN este:
DN = Tpi + N
Tu = 15 + 100 2,55 = 270[min/lot] .
4.2.7 Elaborarea programului cu comanda numerica
4.3 Proiectarea
operatiei numarul 20 - Strunjire II
4.3.1
Intocmirea schitei operatiei
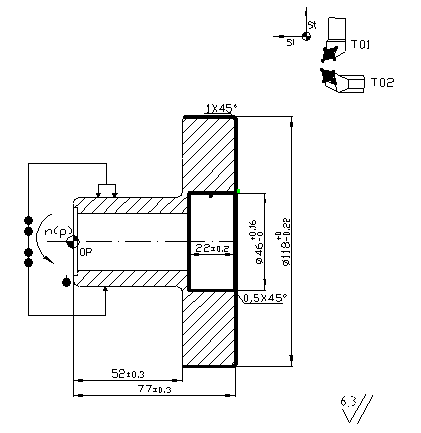
4.3.2
Precizarea fazelor de lucru ale operatiei
A. Orientarea
si fixarea semifabricatului in dispozitiv ;
1. Strunjire de degrosare
suprafata la cota 77mm;
2. Tesire la
1x45°;
3. Strunjire de
degrosare cilindrica exterioara la cota Ĝ117,89mm;
B. Indexare
turela;
4. Tesire la 0,5x45°;
5. Strunjire de
degrosare cilindrica interioara la cota Ĝ46mm;
6. Strunjire de
degrosare suprafata frontala la cota 55mm;
C. Desprins
semifabricat din dispozitiv.
Tabel 4.9
Schita
operatiei
|
Punctele
caracteristice/ coordonatele
|
X
|
Z
|
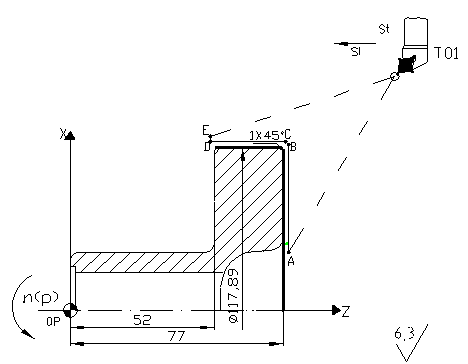
|
A
|
|
|
B
|
|
|
C
|
|
|
D
|
|
|
E
|
|
|
|
N01 G36 XZ
T01 01 M03 M06
N02 G00 G96 X40
Z 79
N03 G01 X 46
Z77
N04 X115.89
N05 X117.89
Z76
N06 Z50
N07 X120
N08 G00 Z79
|
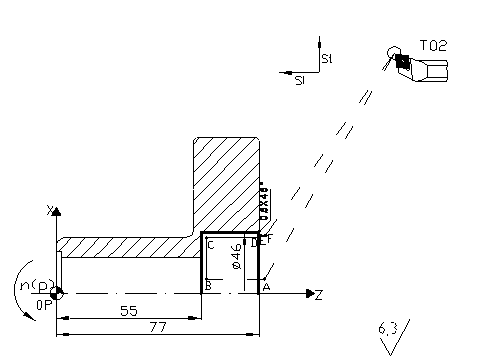
|
A
|
|
|
B
|
|
|
C
|
|
|
D
|
|
|
E
|
|
|
F
|
|
|
N09 G36 XZ
T02 02M06
N10 G00 G96
X25 Z79
N11 Z55
N12 G01 X46
N13 Z76.5
N14 X47 Z77
N15 Z79
N16 G00 X120
|
| | | | |
4.3.3 Stabilirea principalelor caracteristici ale elementelor
sistemului tehnologic
Masina-unealta:
GT 400 Strung cu
comanda numerica(idem operatiei 10).
Dispozitiv
de orientare si fixare a piesei: universal cu trei bacuri;
Sculele de
prelucrare sunt:
cutite normale de prelucrare prin aschiere, formate din suport
si placute schimbabile din carburi metalice, specifice
prelucrarilor ce se executa (degrosare/finisare suprafete
exterioare si interioare);
Cutitul
T01:
Placuta CNMG 09 04 08-PM, avand dimensiunea
caracteristica de 9.525 mm si grosimea placutei de
4.76 mm.
Suport: PCLNL 16 16 H 09, cu dimensiunea caracteristica a
placutei de 9.525 mm.
Nuanta de carbura a placutei: GC 4025.
Sistemul de prindere: T-MAX P Lever.
Cutitul
T02:
Placuta CNMG 09 04 08-PM ; avand dimensiunea
caracteristica de
9.525 mm si grosimea placutei de 4.76 mm.
Suport:SCLCL 16 16 H 09 , cu dimensiunea caracteristica a
placutei de 9.525 mm.
Nuanta de carbura a placutei: GC 4015.
Sistemul de prindere: T-MAX U Screw
4.3.4 Stabilirea metodei de reglare la dimensiune a sistemului
tehnologic
Metoda de reglare a sistemului
tehnologic: se face cu
piesa de proba.
4.3.5 Determinarea valorilor parametrilor regimului de lucru
Tabel nr..4.10
Valorile regimului de
aschiere pentru fiecare etapa in parte
Etapa
|
Caracteristicile
sculei
Sistemul
de prindere
|
Suprafata
|
D
[mm]
|
t
[m]
|
L
[mm]
|
Ra
[μm]
|
Tb
[min]
|
s
[mm/ro]
|
Vc
[m/min]
|
n
[rot/min]
|
P
[KW]
|
I
|
CNMG
09
03 08-PM
T-MAX
P Lever
|
S1
|
|
|
|
|
|
|
|
|
|
S4
|
|
|
|
|
|
|
|
|
|
II
|
CNMG
09
03 08-PM
T-MAX
U Screw
|
S16
|
|
|
|
|
|
|
|
|
|
Stabilirea
componentelor ciclului de munca si determinarea normei de timp
Timpul de baza :
Tb = (tb + ti)
· 1.1 = [( 29+10+15+3) + 4·2] · 1.1 = 71,5cmin
tb
-timpi de baza pentru fiecare faza a operatiei;
ti
- timpul de indexare.
Timpul
auxiliar-manual:
Ta = 97 cmin (include timpul de
apucare a semifabricatului, de fixare in dispozitiv si de pornire a
masinii-unelte);
Timpul mascat:
Tma = 15 cmin (timpul de
control al piesei)
Timpul de pregatire-incheiere:
Tpi = 15 min/lot
Timpul unitar (care se consuma identic
pentru realizarea unei piese):
Tu = Tb + Ta +Tma = 71.5+ 97+15 =183cmin/buc =1,83 min/buc
Norma de timp pe operatie:
TN = Tu + Tpi/N =
1,83 + 15/100 = 1,98 min/buc
Durata necesara executarii lotului piese, DN:
DN = Tpi + N Tu = 15+ 100 1.98= 198 min/lot
4.3.7 Elaborarea programului cu comanda numerica
4.4 Proiectarea
operatiei numarul 30 -Gaurire
4.4.1
Intocmirea schitei operatiei
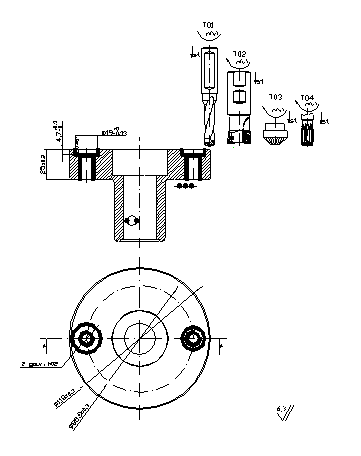
4.4.2 Precizarea fazelor de lucru ale
operatiei
A. Orientare si fixare semifabricat in dispozitiv
B. Indexare turela
1.Gaurire succesiva la cota Ĝ10,2x25
C. Indexare turela
2. Adancire succesiva la cota Ĝ 19x4,7
D. Indexare turela
3.Tesire succesiva la cota1x45°;
E. Indexare turela;
4. Filetare succesiva M12x1,25
F. Desprindere semifabricat
4.4.3 Stabilirea principalelor caracteristici ale elementelor
sistemului tehnologic
Masina unealta Masina
de gaurit cu comanda numerica GPR 45 :
Diametrul maxim de
gaurire in otel cu τr = 50 . 60 daN/mm . . . . ..45
Cursa verticala a
papusii . . . . . . . . .mm . . . . . . . . 500
Cursa
longitudinala a saniei . . . . . . . mm . . . . . . . . . 420
Cursa
transversala a mesei . . . . . . . ..mm . . . . . . . . . 710
Suprafata
utila a mesei . . . . . . . . . mm . . . . . . . . 500x800
Nr. de locasuri de
scule in capul revolver . . . . . . . . . . . .6
Nr. treptei de
turatii . . . . . . . . . . . . . . . . . . . . . .12
Domeniul turatiilor
. . . . . . . . . . ..rot/min . . . . . . .56..2500
Domeniul
avansurilor(variabil continuu) . . mm/min . . . . . . 44000
Puterea motorului
principal . . . . . . . ..kw . . . . . . . . . ..4
Masa masinii
. . . . . . . . . . . . . .kg . . . . . . . . . .5000
Dimensiunile de gabarit:
Lungimea
. . . . . . . . . . . . . . .mm . . . . . . . . . 2085
Latimea
. . . . . . . . . . . . . . . mm . . . . . . . . . 1990
Inaltimea
. . . . . . . . . . . . . . mm . . . . . . . . . .2770
Accesorii:
masa rotativa;
dispozitiv de gaurire rapida;
microscop de centrare;
dispozitiv de prereglare a sculelor.
Dispozitiv de orientare si fixare a piesei:dispozitiv special de gaurit
indexabil.
Scula utilizata
T01 - burghiu scurt cu coada cilindrica de tip
N STAS 573- 80, simbol A1 avand urmatoarele caracteristici:
unghiul de asezare : a = 140 [tabel 3.3]
unghiul de inclinare a taisului
transversal : w
unghiul la varf : - 2c
lungimea fatetei ajustate: fn= 0,2
unghiul de asezare la portiunea
fatetei : a
diametru = f
L=133 [mm] ;
l =87[mm] [tabel 3.17]
T02 - adancitor conic cu coada conica si
STAS 1367/2-78 avand urmatoarelecaracteristici:
D= 19[mm];
d1= 12,5[mm];
L=100[mm];
l1= 22[mm];
l2=40[mm].
T03 - adancitor conic (tesitor)cu unghiul la varf de
90° cu coada conica, STAS 1367/1-78, avand lungimea totala, L=93
[mm] si lungimea partii active, l= 20 [mm] realizat din
otel Rp3. Diametrul D=19 [mm], iar d=3,2 [mm].
T04 - tarod de forma B, STAS 112/8-75, care are
urmatorii parametrii geometrici si elemente constructive ale
partii aschietoare a tarodului:
Con de atac: mediu, cu tais
suplimentar inclinat, pentru gauri de trecere;
Lungimea conului de atac: 4P= 12 [mm];
Diametrul nominal d= M12=10,2 [mm];
Numarul de dinti P=4;
Tarod pentru filet metric;
Diametrul minim al conului de atac d3=d-1,2P=6,8
[mm];
Rezistenta la rupere, Rm = pana
la 400 [N/mm2];
Unghiul de degajare: γp=13°ħ1°.
Dipozitivul de orientare si fixare utilizat in procesul tehnologic al acestei
piese este un dispozitiv special de gaurit.
Verificatoarele utilizate : calibre.
4.4.4 Stabilirea metodei de reglare la dimensiune a sistemului
tehnologic
Metoda utilizata este
metoda de reglare automata la dimensiune.
4.4.5 Determinarea valorilor
parametrilor regimului de lucru
T01 - burghiu scurt cu coada cilindrica de tip
N STAS 573- 80:
1. Adancimea de aschiere
Se determina
cu ajutorul relatiei:
T = D/2 , in care D este diametrul gaurii de executat
T= 5,1mm
2. Durabilitatea economica
Se adopta din normative
Tec= 12min [tabel 6.1]
3. Uzura admisibila ha= 0.4mm[tabel 6.2]
4. Uzura admisibila a placutelor burghiului ha= 0.4 mm [talel 6.3]
5. Avansul de aschiere
Se adopta din normative
s=0.15
6. Viteza de aschiere
Cv=5 ; zv =0,4; mv= 0,2; yv=0,7; Kv=1
v=30,11 m/min
7. Turatia sculei
Se determina cu ajutorul relatiei:
n = (1000 x V)/ (p x D) [rot/min]
n=940rot/min
Din caracteristicile masinii se adopta turatia nr=950rot/min
8. Viteza reala :
vr= pxDxnr/1000 [m/min]
vr= 30,42m/min
9. Forta axiala :

CF =74; xF=1; yF=0,7; KF =1
F= 196,24[daN]
10. Momentul :

CM=29,6; yM= 1.9
M=512,63daN/m;
11.Verificarea puterii motorului electric
Se determina cu ajutorul relatiei:
P= M xv (3060x Dxη) [KW]
P= 0,62 KW
T02 - adancitor cu coada conica STAS 1367/2-78 :
1. Adancimea de aschiere
Se determina
cu ajutorul relatiei:
t = (D-d)/2 , in care D este diametrul gaurii de
executat
t= 4,4mm
2. Durabilitatea economica
Se adopta din normative
Tec= 18min [tabel 6.4]
3. Uzura admisibila ha= 0.2mm[tabel 6.5]
4. Uzura admisibila a placutelor burghiului ha= 0.2 mm [talel 6.5]
5. Avansul de aschiere:
Se adopta din normative
s=0.7mm/rot
6. Viteza de aschiere
Cv=16,3; zv =0,3; mv= 0,3; yv=0,5; Kv=1
v=14.42 m/min
7. Turatia sculei
Se determina cu ajutorul relatiei:
n = (1000 x V)/ (p x D) [rot/min]
n=241,70 rot/min
Din caracteristicile masinii se adopta turatia nr=250
rot/min
8. Viteza reala :
vr= pxDxnr/1000 [m/min]
vr= 14,91 m/min
9. Forta axiala :

CF =7; xF=0.95; yF=0,7; zF=0.,5 ; KF =1
F= 14,93 [daN]
10. Momentul :

CM=105; yM= 0.75; zM=1
M=95,66daN/mm
T03 - adancitor conic (tesitor)
T04 - tarod
4.4.6 Stabilirea componentelor
ciclului de munca si determinarea normei de timp
Tabel 4.12
Denumire piesa
|
BUCSA
|
Nr. si denumire
operatie
|
| |
Material piesa
|
OLC 45
|
Masina-unealta
|
| |
Nr. crt.
|
Denumirea activitatii
|
S.D.V. - urile
utilizate
|
Regim de aschiere
|
Timpi [ cmin]
| |
v
|
f(s)
|
n
|
a(t)
|
i
|
vf
|
L
|
tb
|
tam
|
ta
|
tma
|
tf
| |
|
Prindere
SF (din container)
|
Bolt
cilindric scurt
Cepi
pentru suprafata plana
Burghiu
Ĝ10,2
Adancitor
Ĝ19
Adancitor
conic
Tarod
Calibru
|
|
|
|
|
|
|
|
|
|
|
|
| |
|
Orientare
- fixare SF in dispozitiv
|
|
|
|
|
|
|
|
|
|
|
|
| |
|
Pornire
rotatie arbore principal
|
|
|
|
|
|
|
|
|
|
|
|
| |
|
Cobarare
arbore principal 80 mm
|
|
|
|
|
|
|
|
|
|
|
|
| |
|
Indexare
cap revolver T01
|
|
|
|
|
|
|
|
|
|
|
|
| |
|
Cuplare
avans de lucru
|
|
|
|
|
|
|
|
|
|
|
|
| |
|
Gaurire
prima gaura
|
|
|
|
|
|
|
|
|
|
|
|
| |
|
Retragere
automata scula
|
|
|
|
|
|
|
|
|
|
|
|
| |
|
Indexare
dispozitiv
|
|
|
|
|
|
|
|
|
|
|
|
| |
|
Cuplare
avans de lucru
|
|
|
|
|
|
|
|
|
|
|
|
| |
|
Gaurire
a doua gaura
|
|
|
|
|
|
|
|
|
|
|
|
| |
|
Retragere
automata scula
|
|
|
|
|
|
|
|
|
|
|
|
| |
|
Indexare
cap revolver T02
|
|
|
|
|
|
|
|
|
|
|
|
| |
|
Cuplare
avans de lucru
|
|
|
|
|
|
|
|
|
|
|
|
| |
|
Adancire
prima gaura
|
|
|
|
|
|
|
|
|
|
|
|
| |
|
Retragere
automata scula
|
|
|
|
|
|
|
|
|
|
|
|
| |
|
Indexare
dispozitiv
|
|
|
|
|
|
|
|
|
|
|
|
| |
|
Cuplare
avans de lucru
|
|
|
|
|
|
|
|
|
|
|
|
| |
|
Adancire
a doua gaura
|
|
|
|
|
|
|
|
|
|
|
|
| |
|
Retragere
automata scula
|
|
|
|
|
|
|
|
|
|
|
|
| |
|
Indexare
cap revolver T03
|
|
|
|
|
|
|
|
|
|
|
|
| |
|
Cuplare
avans de lucru
|
|
|
|
|
|
|
|
|
|
|
|
| |
|
Tesire
prima gaura
|
|
|
|
|
|
|
|
|
|
|
|
| |
|
Retragere
automata scula
|
|
|
|
|
|
|
|
|
|
|
|
| |
|
Indexare
dispozitiv
|
|
|
|
|
|
|
|
|
|
|
|
| |
|
Cuplare
avans de lucru
|
|
|
|
|
|
|
|
|
|
|
|
| |
|
Tesire
a doua gaura
|
|
|
|
|
|
|
|
|
|
|
|
| |
|
Retragere
automata scula
|
|
|
|
|
|
|
|
|
|
|
|
| |
|
Indexare
cap revolver T04
|
|
|
|
|
|
|
|
|
|
|
|
| |
|
Cuplare
avans de lucru
|
|
|
|
|
|
|
|
|
|
|
|
| |
|
Filetare
prima gaura
|
|
|
|
|
|
|
|
|
|
|
|
| |
|
Retragere
automata scula
|
|
|
|
|
|
|
|
|
|
|
|
| |
|
Indexare
dispozitiv
|
|
|
|
|
|
|
|
|
|
|
|
| |
|
Cuplare
avans de lucru
|
|
|
|
|
|
|
|
|
|
|
|
| |
|
Filetare
a doua gaura
|
|
|
|
|
|
|
|
|
|
|
|
| |
|
Schimbare
sens de rotatie
|
|
|
|
|
|
|
|
|
|
|
|
| |
|
Retragere
automata scula
|
|
|
|
|
|
|
|
|
|
|
|
| |
|
Oprirea
rotatiei arbore principal
|
|
|
|
|
|
|
|
|
|
|
|
| |
|
Ridicare
arbore principal 80 mm
|
|
|
|
|
|
|
|
|
|
|
|
| |
|
Desprindere
semifabricat
|
|
|
|
|
|
|
|
|
|
|
|
| |
|
Depozitare
semifabricat in container
|
|
|
|
|
|
|
|
|
|
|
|
| |
|
Curatare
dispozitiv de aschii
|
|
|
|
|
|
|
|
|
|
|
|
| |
|
Control
piesa (F=1/10 piese )
|
|
|
|
|
|
|
|
|
|
|
|
| |
Ciclograma
operatiei
|
Total
categorii de timp [cmin]
|
|
|
|
|
| |
tf
|
|
|
|
|
|
|
|
|
|
|
|
|
|
|
|
|
|
|
|
|
|
|
|
| |
tma
|
|
|
|
|
|
|
|
|
|
|
|
|
|
|
|
|
|
|
|
|
|
|
|
Timp
de pregatire-incheiere, Tpi [min/lot]
|
|
tb
|
|
|
|
|
|
|
|
|
|
|
|
|
|
|
|
|
|
|
|
|
|
|
|
tma
|
|
|
|
|
|
|
|
|
|
|
|
|
|
|
|
|
|
|
|
|
|
|
|
Timp unitar, Tu
[min/buc] 4,97
|
|
ta
|
|
|
|
|
|
|
|
|
|
|
|
|
|
|
|
|
|
|
|
|
|
|
|
| |
|
Scara
timpului [cmin]
|
Norma de timp, TN
[min/buc]
|
| |
|
|
| |
Numar
de piese pe lot [buc]
|
|
Durata executiei lotului de
piese, [min/lot]
|
| |
| | | | | | | | | | | | | | | | | | | | | | | | | | | | | | | | | | | | | | | | | |
4.5 Proiectarea
operatiei numarul 40 -Brosare
4.4.1
Intocmirea schitei operatiei
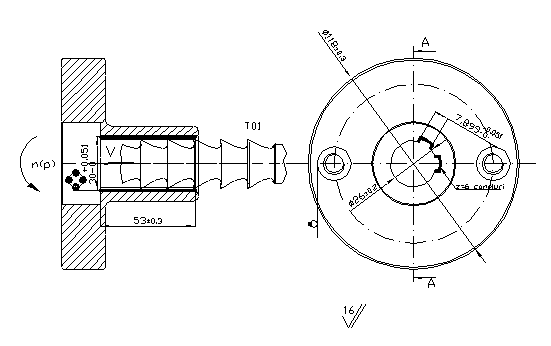
4.5.2 Precizarea fazelor de lucru ale
operatiei
A.Orientare si fixare semifabricat
1. Brosare caneluri la cota 7,899x Ĝ26
B. Desprindere semifabricat
4.5.3 Stabilirea principalelor caracteristici ale elementelor
sistemului tehnologic
Masina unealta:
Tabel 4.13
Masina
de brosat interior 7A520 cu urmatoarele caracteristici:
|
Valori
|
forta de
tragere, daN
|
|
cursa de lucru,
minima/maxima, mm
|
|
diametrul gaurii
in plansaiba, mm
|
|
vitezele cursei de
lucru, m/min
|
|
puterea
actionarii hidraulice, kW
|
|
Scula
utilizata: Brosa din Rp3, cu:
lungimea
totala 420 [mm];
suprainaltarea
dintilor, a = 0,025 [mm];
pasul dintilor
aschietori, p = 12 [mm]
parametrii geometrici
ai brosei: γ = 12° ; α = 3°
Dispozitivul de orientare si fixare a piesei Dispozitiv de lucru
Verificator micrometru de interior cu valoarea diviziunii de 0,001 mm
4.5.4 Stabilirea metodei de reglare la dimensiune a sistemului
tehnologic
Din constructia brosei
4.5.5 Determinarea valorilor parametrilor regimului de lucru
Durabilitatea
economica Tec= 150[ min];
Avansul pe dinte sd=0,075[
mm];
Viteza de aschiere
:v= 2,4[m/min] ;
Forta de
aschiere de 1 mm lungime a taisului brosei :=23,5[
daN/mm2]
4.5.6 Stabilirea componentelor
ciclului de munca si determinarea normei de timp
Timpul de baza : Tb = =0,18 unde:
Lb
este lungimea activa a brosei , in mm
v este viteza principala
executata de brosa in [m/min]
Timpul auxiliar: Ta= [min](include timpul
pentru
prinderea si desprinderea semifabricatului, timpul pentru curatarea
de aschii a broselor si timpul pentru masuratori de
control )
Timpul frecvential: Tf= 0,4[min] (timpul de
control al piesei)
Timpul de pregatire-incheiere: Tpi
= 28,5 [min/lot]
Timpul unitar (care se consuma identic
pentru realizarea unei piese):
Tu = Tb + Ta +Tf = 0,18+0,235+0,4= 0,815 [min/buc]
Norma de timp pe operatie: TN = Tu + Tpi/N
= 0,815+ 28,5/100 = 1,1 [min/buc]
Durata necesara executarii lotului piese, DN:
DN =
Tpi + N Tu = 28,5 + 100 0,815=
110 [min/lot]
4.6
Proiectarea operatiei numarul 50 -Rectificare cilindrica exterioara
4.6.1 Intocmirea
schitei operatiei
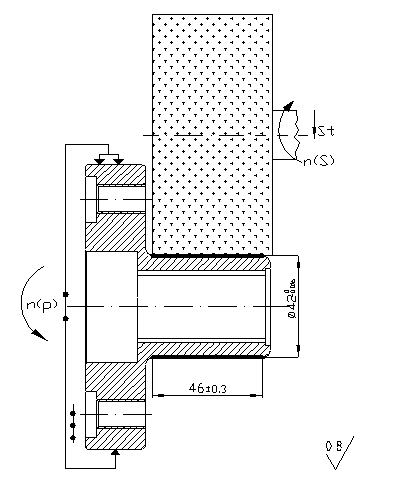
4.6.2 Precizarea fazelor de lucru ale operatiei
A. Orientare si fixare
1.
Rectificare cilindrica exterioara Ĝ 42
B. Desprindere piesa
4.6.3 Stabilirea
principalelor caracteristici ale elementelor sistemului tehnologic
Masina unealta
Tabel
nr. 4.14
Caracteristicile
masinii WMW500
Caracteristici
masina de rectificat interior si exterior WMW 500
|
Valori
|
distanta intre varfuri,
mm
|
|
inaltimea
intre varfuri,mm
|
|
inclinatia
mesei
|
|
diametrul
pietrei exterior, mm
|
|
latimea
pietrei, mm
|
|
puterea
motorului, kW
|
-
piatra interior 0,8
-
piatra exterior . 2.0:3.2
|
numarul de
rotatii pe minut
|
-
piatra interior 11000
-
piatra exterior 1900
|
viteza de inaintare a
mesei, m/min
|
|
Dispozitivul de orientare si fixare a piesei
Dispozitiv de lucru
Verificator: micrometru de exterior cu valoarea
diviziunii de 0,002 mm; rugozimetru
Scula
utilizata: corp
abraziv cilindric plan 1-300x50x127- STAS 601/1-84
4.6.4 Stabilirea metodei de reglare la
dimensiune a sistemului tehnologic
Metoda utilizata este metoda de reglare
automata la dimensiune.
4.6.5 Determinarea valorilor parametrilor
regimului de lucru
1. Adancimea de aschiere
T = Ap = 0.15 mm
2. Durabilitatea economica
Tec = 6 min
3. Adancimea de aschiere si nr de treceri
Din normative alegem o adancime de aschiere
corespunzatoare unei treceri
t = 0,02 mm Tnr de treceri va fi:
i =
Ap/ t = 0,15/0,02 = 7.5≈8 treceri
4. Viteza de aschiere si avansul
Din normative alegem viteza V = 25 m/s
6. Turatia sculei
n = (60000 x v)/ (p x D) = (60000 x 25
)/ (3,14 x 300) = 1592,35 rot/min
n < n meT n me n=1900rot/min
Viteza reala de aschiere: V = (p x D x nr)/60000 = 29.83 m/min
7. Viteza de avans ( circular) a piesei
Din normative alegem viteza de avans circular a piesei
Vs = 30[m/ min]
8.Calculam turatia piesei:
np = (1000 x v)/ (p x d) = (1000 x 30)/
(3,14 x 42) = 227.47rot/min
Din caracteristicile masinii-unelte se alege turatia piesei
np = 220[rot/min]
Viteza de avans va avea expresia:
Vsr = (p x d x np)/ 1000 = (3,14 x 42 x 220)/1000
=29 m/min
9. Verificarea puterii
Alegem din normative puterea efectiva Pe = 3.2 kw,
care se corecteaza cu coeficientii:
K1 = 0,8 in functie de latimea si
duritatea piesei
K2 = 0.9 in functie de diametrul piesei
TPr = Pe x K1 x K2 = 3.2x 0,8 x0.9 = 2.30 Kw
PM.U= 3.2 kw
Pr < PM.U T prelucrarea se poate
realiza pe WMW 500
4.6.6 Stabilirea
componentelor ciclului de munca si determinarea normei de timp
Timpul de baza : Tb = (L / np)∙
(h/t) x K [min] unde
L= l-(0.2.0.4)x Bd= 46 -0.35x50=28,5
l- lungimea de rectificat (46)
Bd- latimea discului (50)
np - turatia piesei (200 rot/min)
h- adaosul de prelucrare pe raza (h= 0.15)
t - adancimea de aschiere la o trecere
(t=0.02 mm/ trecere ) K=1.3
Tb= (28,5 /220)∙(0,15/0.02) x 1.3 =
1,26 min
Timpulauxiliar-manual:
Ta= min(include timpul pentru
prinderea si desprinderea semifabricatului, timpul pentru apropierea sculei de
piesa, timpul pentru cuplarea tuartiei piesei, timpul pentru masuratori de
control)
Timpul mascat: Tma = 0,70min (timpul de control al
piesei)
Timpul de pregatire-incheiere:Tpi
= 17 min/lot
Timpul unitar (care se consuma identic
pentru realizarea unei piese):
Tu = Tb + Ta +Tma = 1,26+ 0,6+0,70 = 2,56 min/buc
Norma de timp pe operatie:
TN = Tu + Tpi/N =
2,56+ 17/100 = 2,73min/buc
Durata necesara executarii lotului piese, DN:
DN = Tpi + N Tu = 17 + 100 2,56= 273 min/lot
 |
|
Tehnica mecanica
|
|
|
Analize pe aceeasi tema
|
|
Ramai informat |
Informatia de care ai nevoie Acces nelimitat la mii de documente. Online e mai simplu. |
Contribuie si tu!
Adauga online documentul tau.
|
|
|
|
|